Metal Inert Gas welding, also known as MIG, has seen some great innovations over the last 40+ years.
Modern technology facilitates some excellent new techniques to help with making the process cleaner, more effective, faster, and stronger. What’s not to love?
Let’s dig in.
MIG Welding: How it Works
Basic MIG welding is fairly simple. You have a torch with a wire feeder, and the wire acts as the electrode for an electric current. The electrode conducts the arc into the workpiece, melting in the process and becoming part of the weld pool along with the workpieces. Together, they solidify into a weld, ideally free of pocks or inclusions, and stronger than the original materials.
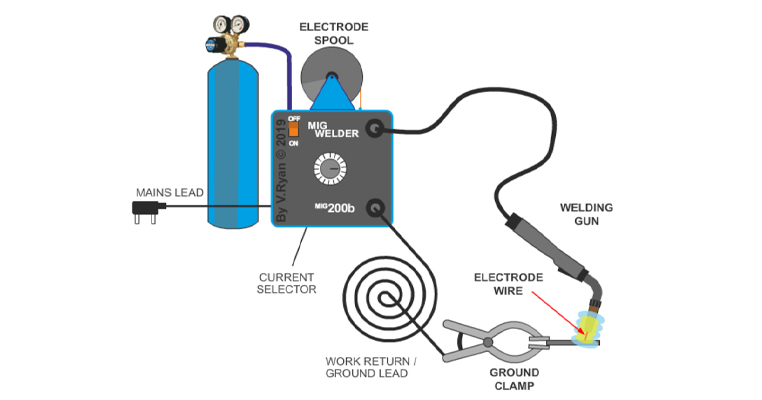
MIG comes in two forms: short circuit and spray. In order to understand pulsed MIG, you need to know how these two variations work and their pros and cons.
Short Circuit MIG Welding
Short circuit MIG welding is the simplest kind of MIG welding. With this form of the process, the workpiece is grounded by using a ground clamp.
Electricity pushed into the welding torch flows to the electrode and, when the electrode touches the workpiece, short circuits through the ground. This flash of arc heats up and melts the electrode until enough of it melts away that the circuit breaks, leaving a molten pool of metal where the electrode contacts the workpiece.
In another process, like stick welding, you would then need to manually adjust the position of the welding torch and the stick of filler metal and tap again to create the circuit arc and melt more metal into the next bit of joint. However, with MIG machines, the wire electrode is fed in automatically, creating a constant, repeated short circuit and allowing you to weld much more quickly and evenly.
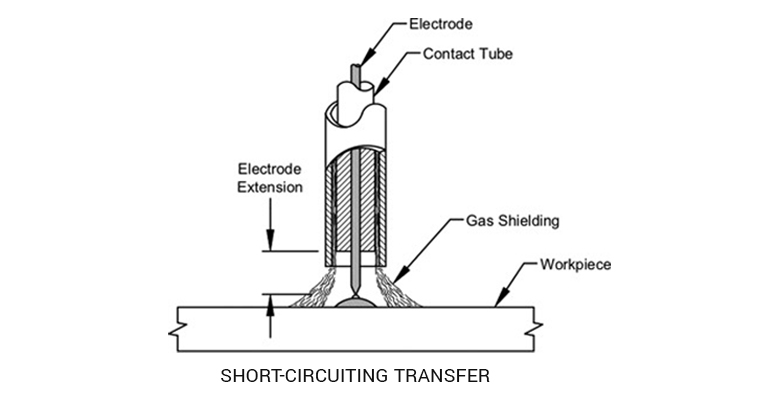
All of this is protected from inclusions and contamination via the use of shielding gas. The result is, ideally, a solid weld with metal free of inclusions and other problems.
The biggest benefit of short circuit MIG is that it can be used in any position, including vertical and overhead. Because each “tap” of the circuit is brief, the weld pool doesn’t stay molten for long, and there’s no continuous arc that can make things more dangerous for an operator.
Unfortunately, short circuit MIG has one significant problem: it’s messy. Each short circuit is a tiny explosion of power and that creates an outward force, creating a spatter. This kind of MIG welding is very easy to learn and is a common “basic” protocol, but it requires a bunch of cleanup and rarely looks good in its base form.
It’s very functional, though, and can be used on any thickness of steel.
Spray MIG Welding
The alternative to short circuit MIG welding is spray MIG welding. It was first developed when someone asked the question: “What happens if you crank up the speed of the wire and the voltage of the welding machine?”
The answer: the arc is created before the electrode even has a chance to contact the workpiece due to the higher voltage. Faster wire feed speed causes the electrode to melt almost before it leaves the torch, and the resulting molten metal is literally sprayed via the powers of electricity, the shielding gas, and gravity to the location of the weld.
In a way, you can think of the difference between these two as sort of like the difference between painting a surface using a brush versus using spray paint, though the analogy isn’t actually very accurate when you consider the mechanics behind them.
Spray transfer MIG has a number of distinct advantages over short circuit MIG welding. Primarily, it’s much cleaner; there’s no spatter to deal with, and it can be used on aluminum because of the comparatively lower heat at the site of the weld. It requires a more-pure shielding gas (usually 90%+ Argon) to achieve a quality and consistent spray.
There are, unfortunately, a few downsides to this process as well. Though it is cleaner and more effective on certain materials than short circuit transfer, the fact that the molten metal from the electrode is literally spraying across open air means that the process can’t be used in vertical or overhead positions. Trying to do so will result in poor quality transfer as much of the molten metal falls back down or drips, leaving shallow, inconsistent welds and risking burns or injuries to the operator.
Enter Pulsed MIG Welding
This is where pulsed MIG welding comes into play. What is it, though?
Imagine if you could get flexibility in the positioning of short circuit welding but the cleanliness and speed of spray transfer out of one single process. It’d be great, right? Well, luckily, you can.
Pulsed MIG welding was first developed in the 1980s using advancements in electronic control technologies.
Instead of having one solid amperage across the board while you’re welding and controlling the frequency of contact/arc via the speed of wire feeding, pulsed MIG uses electronic components to set two amperages; a peak amperage and a background amperage.
The background amperage is a lower amperage that is the baseline minimum your machine puts out at all times. This “flickering” of the voltage has a few effects.
First, the background amperage never dips below a determined minimum. This provides a solid baseline and enforces a constant arc while reducing the overall amount of heat going into the weld puddle. This is how it can be used in positions other than horizontal, and it makes it flexible enough to use overhead.
The peak amperage, meanwhile, is the higher amperage necessary to flash-melt and spray the electrode as you would in spray transfer. This gives your weld bead the cleanliness and consistency of a spray transfer without the limitations caused by high heat in a standard spray.
Unlike traditional spray transfer that is primarily controlled by rapid wire feed speed, pulsed MIG welding uses electronic components to create a square wave in the electrical current, with a frequency (measured in hertz) of anywhere from a few times per second to hundreds of times per second.
The biggest drawback to pulsed MIG is that it requires a highly skilled operator. While the process itself is not difficult, knowing how to set the base and peak amperages, feed speed, gas flow rate, and other settings requires a lot of experience or a solid reference document for consistent projects.
At least, that was the case in the 80s, 90s, and early 2000s. In modern times, the operator doesn’t need to have an encyclopedic knowledge of various factors and configurations to use pulsed MIG as a process.
Modern MIG machines have a wide range of programs that can be selected based on key attributes of a configuration, essentially allowing an onboard computer to do the thinking for you.
This has made pulsed MIG infinitely more accessible to casual operators and has made it often a go-to process today.
What is Double Pulsed MIG Welding?
If pulsing the current is good at making a welding process more effective, what if you pulsed it again?
While this might sound like pseudoscience nonsense, it’s actually easily achievable with signal alterations and is done in a wide variety of settings with a wide range of technologies. It’s not limited just to welding, not by a long shot.
One of the features of a square wave is that an additional square wave of another frequency will add and remove from the base square wave. While in uncontrolled signals, this amounts to noise, it can be highly beneficial when carefully controlled.
For example, check out this signal diagram. In this diagram, you can see the primary square pulse, with the blue upper amperage and the orange lower amperage. However, throughout the entire signal, there’s a smaller square wave at a higher frequency that adds and removes from the base signal.
To put it in numerical terms, you might have patterns like these:
- Single Pulsed: 10, 5, 10, 5, 10, 5, 10, 5…
- Double Pulsed: 10, 9, 10, 9, 10, 5, 6, 5, 6, 5, 10, 9, 10…
This additional pulsing of the electrical current allows the welding machine to give the operator even more exceptional control over the weld bead. In fact, the welds it makes can look almost like TIG welds, with that characteristic “stack of dimes” appearance that is so sought-after aesthetically in many welds.
Unlike TIG, a double-pulsed MIG still uses a consumable electrode and still results in the basic spray transfer operation, along with the faster transfer speeds of MIG over TIG.
This leaves you with a strong, solid, and highly aesthetically pleasing final weld bead.
The greatest downsides to double-pulsed are similar to what single-pulsed used to be; that is, it’s very complicated and requires a lot of knowledge to set properly. With so many settings and configurations that need to be exactly right, it’s very easy for a project to fail because of an improper setting.
As such, many double-pulsed machines actually “fix” some of the settings. The secondary pulsing, for example, might be locked or might only be toggled between a couple of standard settings as designed by the developers of the machine.
Of course, the development that goes into creating these settings, and the computerization required to control the configuration, means that welding machines capable of double-pulsed MIG welding tend to be much more expensive than machines capable of single-pulsed or basic no-pulsed MIG welding. The increases in efficiency and speed can be worth that added cost, but the startup costs and training required to do it are much steeper.
Why Isn’t Double-Pulsed MIG The Standard?
Given all of the advantages of double-pulsed MIG, you might wonder why it isn’t standardized yet.
The answer comes from several different angles.
The first is that, as a relatively new development in MIG technology, it’s both somewhat expensive and in need of more testing and development. That’s not to say it’s dangerous – no more so than any welding process, and less than some – but that companies still aren’t entirely sure of what the best configurations are for specific tasks. Some tasks may also fall outside of standard configurations, which means operators might want unlocked machines, which have many more potential points of failure.
Similarly, many companies are coming at the process from different angles and with different forms of development. That means machines you get from one company may not share settings or configurations with other company machines, and even the terminology is different. In part, this is due to different development processes, but it’s also in part just companies trying to find a name that catches on so they can claim it as their trademark.
At the same time, welding as an industry is rarely quick to embrace change. There are many old hand operators out there who insist on stick welding as the best process. Whether it’s resistance to change, resistance to the expense of new machines, or simply a desire to wait to see what settles out as the “best” option, many shops are hesitant to invest in the newest technologies.
That said, double-pulsed MIG, used in conjunction with welding automation systems and even computerized fabrication machines, can create exceptionally consistent end products with fast throughput, efficient use of electrode wire and other consumables, and other benefits.
How to Get Started with Pulsed MIG Welding
The best way to get started with pulsed MIG and double-pulsed MIG is to obtain a welding machine that can handle it and simply give it a try. You don’t have to outright buy a new welding machine, however.
That’s where we come in. Our welding equipment rentals offer the option to try anything before you spring for a full purchase. And, if you like what you try, you can even buy our used welding equipment.
Whether you need small-scale welding equipment for a single shop or a complete, automated solution for spinning up a fabrication facility, we’ve got you covered. Reach out and talk to our sales and service teams to set you up with the solution to any welding needs you may have at any scale.
Leave a Reply