Welding in remote areas is essential for nationwide infrastructure, but it comes with unique challenges. The lack of infrastructure, electrical fluctuations, and the lack of skilled welders are just some of the issues contractors face. However, using the right equipment can alleviate many of these problems. Portable welders, plasma cutters, and diesel engine welders, for example, can make job sites more productive despite these challenges. Read on to learn more about specialized equipment for welding in remote areas.
The Welding Job Diversity in Remote Places
Welding in remote areas can be as exciting as in urban settings. The job types are often different, but there are many opportunities for welders in less populated areas.
Welders work on oil and gas pipelines, vehicle and railway bridges, powerlines, dams, farms, mines, power plants, cellular towers, and construction sites. There are many industries that rely on welding in remote places—far more than one might initially realize.
Challenges Welding Contractors Face in Remote Places
Depending on the industry and welding tasks required, contractors in remote areas can face a wide array of challenges in remote places. It can be incredibly difficult to solve all the issues that arise, but with the right equipment, most problems can be managed or completely eliminated.
Lack of Skilled Welders and CWIs
The global shortage of skilled welders affects everyone, but remote locations often have it worse than urban areas. This issue affects local and out-of-state contractors who need to bring labor to the site. Not all welders want to be relocated for a long periods of time on remote projects.
In addition to welders, the shortage of Certified Welding Inspectors (CWIs) in remote areas can also be a problem. While almost every place has at least several local CWIs, they can be stretched too thin, making their availability an important factor for project development.
Weld automation equipment and advanced process welders can help address both issues. While not all welding can be automated on-site, combining prefabrication with on-site automation can enhance productivity and improve weld quality to help pass the inspection more easily. If the inspectors are presented with near-perfect welds all the time, the inspection is faster, streamlining the process. Defects, on the other hand, slow things down and cause bottlenecks.
Certification for welders, procedures, and machines is also challenging in remote areas, as testing is often done at facilities far from the project site. This poses a big challenge for remote area productivity, as it’s not ideal to wait for test results. That’s what the Red-D-Arc Welder Certification Trailer is designed for. This portable station houses everything required for certification, including a spacious and comfortable office, weld coupon testing equipment, eight welding stations, fume exhaust solution, and other critical equipment.
Unavailability of Electrical Power
Remote places often lack reliable electricity. Welders and other power tools require high electrical power, so it’s critical to use high-performance diesel generators or diesel engine welders.
Power equipment often requires up to five times their running power just to start. So, knowing how to choose a generator is critical for ensuring your team has all the electricity it needs.
Welders working on oil and gas pipelines or infrastructure projects often weld thick pipes and structural components, which requires a lot of power. So, it can also be cost-effective to use diesel-powered welders for welding and diesel generators for other power tools, lights, portable offices, and other less demanding equipment.
For example, the Lincoln Electric Dual Maverick 200/200X Diesel Engine Welder is a phenomenal machine for construction and pipeline welding where electricity is unavailable. This is a dual-output machine that allows two operators to weld simultaneously, which is often needed when welding pipe. Two operators welding the pipe from opposing sides prevents distortion and ensures the joint remains aligned post-welding.
Power Fluctuations
Even when power is available in remote places, it’s important to check the quality of the electrical power. Power fluctuations can pose a challenge when running high-amperage equipment like welding power sources.
Fortunately, modern welding power sources can mitigate this issue. For example, the Miller XMT 350 multi-process welder supports Miller’s Auto-Line Input Power Management, which ensures the delivery of consistent output regardless of the power spikes and dips from the power outlet.
Loss of Productivity Due to Non-Value-Adding Activities
Remote job sites often involve time-consuming, non-value-adding tasks such as handling materials and adjusting equipment. When it comes to welding, a particular loss of productivity is inherently tied to machine output adjustments.
Working on a pipeline in a trench or high up on the bridge structure makes it time-consuming to stop what you are doing and get back to the power source to adjust the voltage or amperage. Now, imagine doing that multiple times during the work shift. This leads to significant time wasted as well as operator fatigue. Depending on the weld pass, joint type, fit-up, material’s heat, and travel speed, it can be necessary to adjust the welding parameters. For example, you can start with more amps, but due to the part heating up during welding, you may need to dial it down slightly.
This problem can be eliminated by using advanced technologies, like Miller’s ArcReach®. Our EX360 FieldPro Multi-Process Welder with ArcReach can improve jobsite productivity. ArcReach allows complete remote control of weld parameters without the control cable. It uses the weld cable to communicate with the power source, preventing accidental tampering with the settings. This technology boosts productivity and ensures compliance with the approved welding procedure specification (WPS).
Having to Shape Metal Structures On-site
While welding prefabrication is highly desirable for remote jobs, it’s often necessary to shape metal structures on-site, especially during decommissioning and demolition.
Our plasma cutter rentals are a perfect choice for highly productive metal cutting. Unlike oxy-fuel, plasma cutters don’t require combustible fuel, drastically reducing the job’s cost and negative safety aspects. Not only do you have to pay for the fuel, but you have to transport and safely store the oxygen and acetylene gas bottles on-site. Plasma cutters only need a portable power source and electrical power, making them more portable and cost-effective.
The Hypertherm Powermax 1650 is a highly portable plasma cutter, reducing both cost and safety risks compared to oxy-fuel setups. Plasma cutting is an excellent alternative for most tasks, though oxy-fuel still has its place in certain scenarios.
We also have a large selection of Hypertherm SYNC plasma cutters. The SYNC technology combines plasma cutter consumables into singular cartridges, each with its own purpose. For example, if you want to gouge, you’d use a gouging cartridge; if you’re going to cut, you’d use a cutting cartridge. The SYNC platform brings much more to the table than just simplified consumable management. For example, it provides RFID communication with the SmartSYNC Hypertherm torches, giving you data like arc starts, arc-on time, and other valuable data.
When it comes to pipe joint preparation, it’s critical to produce consistent cuts and bevel angles. If you use a tool like an angle grinder to bevel the joint, you can never make a completely uniform bevel. This can lead to weld defects like overfill, underfill, or undercuts because the joint can have too little or too much removed material.
Pipe cutters and bevelers are the solution for uniform joint preparation. Tools like the H&S Tool PB8 Power Beveler ensures a smooth, perfect bevel every time. Its rotating blade removes layer upon layer of the pipe while the operator guides it further into the pipe; however, the operator’s movement is mechanically limited. The tool cannot produce an uneven bevel if set correctly.
Working with Various Metals
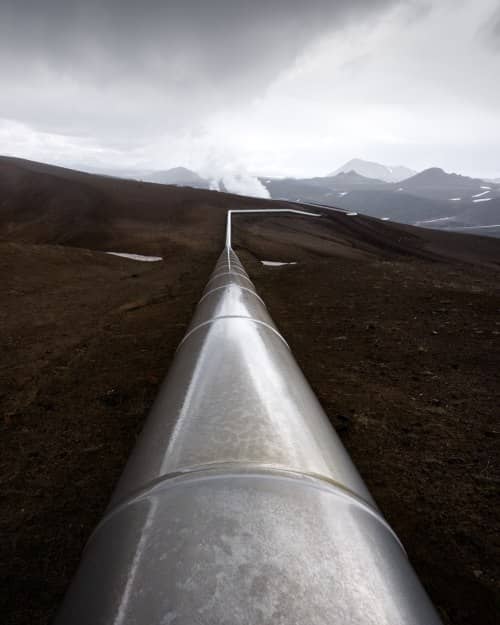
Welding in remote areas often involves a wide variety of metal alloys, from carbon steel to high nickel, aluminum, titanium, and stainless steel. For example, building a typical petrochemical plant can require working with almost all materials in the welding industry.
To stay versatile and productive in such a diverse environment, you can rely on advanced multi-process welders that support MIG, flux-cored, stick, and TIG welding. So, no matter the task, you have a process that can handle it.
We also offer rugged multi-process welders like the Red-D-Arc DC400 or its big brother DC600. Depending on the environment, they can be a preferred solution. However, selecting the multi-process machine comes down to many factors. Don’t hesitate to reach out for help in choosing the appropriate welder for your job.
Having to Apply Preheating and PWHT Procedures On-Site
Whether you are welding structural steel or pipelines, welding codes and procedures often require applying welding preheat and post welding heat treatment (PWHT). However, applying any sort of heat treatment in remote locations can be challenging. While open-flame heating is an option, it can be costly and hazardous.
Resistance heating is complex, time-consuming, requires specialized knowledge, and isn’t always suitable for on-site jobs; however, resistance heating can be used for all materials, making it the most versatile option.
Induction heating systems are the best overall. These systems are portable, energy-efficient, and ideal for on-site jobs involving magnetic materials. Renting induction heating equipment is often the most cost-effective option for remote projects.
We provide the Miller ProHeat 35, a renowned induction heating system. The ProHeat 35 can be air or liquid-cooled and can be applied for most welding jobs. It’s relatively portable, offers exceptional time-to-temperature, provides uniform treatment, and has an easy-to-use interface.
Rent or Lease from Red-D-Arc
Welding in remote areas presents numerous challenges, but almost every problem can be resolved with adequate equipment selection. Of course, not all contractors find it cost-effective to purchase specialized equipment, but if you are planning to take a one-off job that requires powerful diesel generators or other equipment, it’s far more cost-efficient to rent equipment. Red-D-Arc has a massive fleet of welding and cutting solutions ready for you. Contact a member of our team today to find the right equipment to meet your job’s demands and improve productivity.