Welders typically begin their careers working with carbon steel, mild steel, and various iron alloys, which are all relatively similar when it comes to the process and procedure. Over time, they expand their skills to include other metals, such as aluminum, stainless steel, or even entirely different materials.
One metal that holds a certain reputation among welders is titanium. Some view it as an impossible challenge. Others see it as a highly specialized field they have little interest in pursuing. Then there are those who have worked with titanium before—some love it, while others dislike it.
What’s the reality? Is titanium harder to weld than iron and steel? Is it substantially different? We’ve addressed many of the most common questions below. As always, if you have a question we haven’t covered, feel free to ask in the comments or reach out directly. We’re always happy to help.
Why is Titanium Special?
Titanium is special because it possesses relatively unique properties. There are three key attributes that make it highly sought after, particularly in specific applications.
First, it’s very strong. Steel can be stronger—it’s not a miracle metal—but titanium is strong and resilient in ways that are ideal for uses like biomedical implants, aerospace construction, and more.
Strength alone isn’t enough, though. The real benefit of titanium is that it offers that strength at a much lower weight and size than comparably strong steel. This makes it ideal for applications where weight is crucial, such as in airplanes, drones, or any structure that needs to be lightweight yet durable. A titanium frame can be thinner, lighter, and more durable than a steel frame designed for the same purpose.
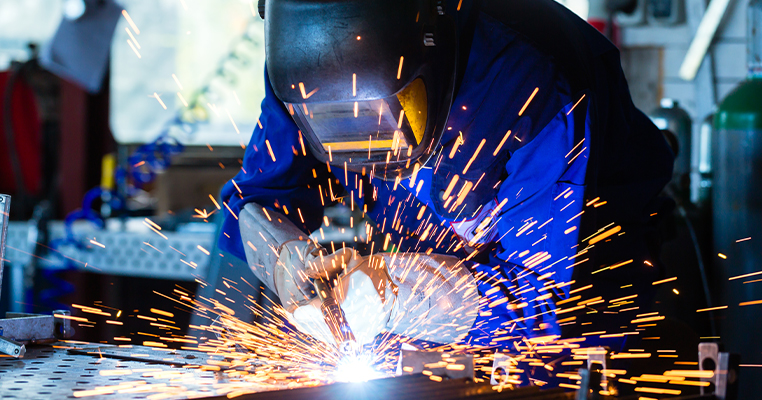
The third benefit of titanium is its resistance to corrosion. While it can be corroded by a very strong acid, high temperatures, or specific chemicals, it resists most forms of corrosion naturally. This is why it’s used in environments like marine settings and applications such as hip replacements.
These three benefits combine to make titanium one of the most useful metals in a wide range of high-stakes applications.
Why Isn’t Titanium More Widely Used?
If titanium has so many excellent properties, why isn’t it used more often? Why do we still rely on steel for basic construction and other purposes?
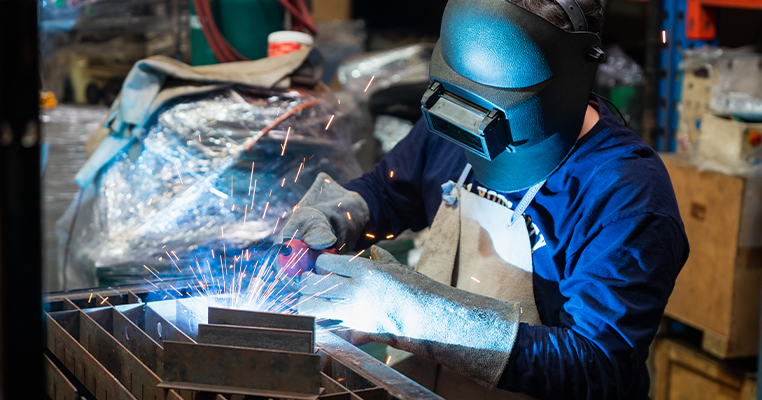
There are several key reasons.
Titanium has a high degree of reactivity during the manufacturing process. If it’s not processed properly, it can develop impurities and inclusions that are virtually impossible to remove, which can cause critical faults in the finished product.
It’s not suitable for high-temperature uses. Anything over about 400 degrees Celsius can cause titanium to lose its strength, whereas standard steel can resist these temperatures more effectively, and other alloys outperform both.
Titanium is relatively rare and difficult to extract from the earth. The process of turning titanium ore into usable stock is complicated and costly.
The complexity of extraction, refinement, and manufacturing makes titanium a very unforgiving material. Any mistake during the process can ruin the workpiece. As a result, titanium is much more expensive than other materials.
There are important use cases for titanium, but there are just as many cases where it’s financially infeasible to use.
What is the Greatest Challenge with Titanium Welding?
Titanium welding presents several challenges, but by far the biggest is oxygen embrittlement.
When welding, heat is applied to the metal, which changes its chemical properties. Some materials are more reactive when heated compared to when they are cold. Titanium, unfortunately, is extremely susceptible to oxygen. And, as you might know, oxygen is everywhere around us all the time.
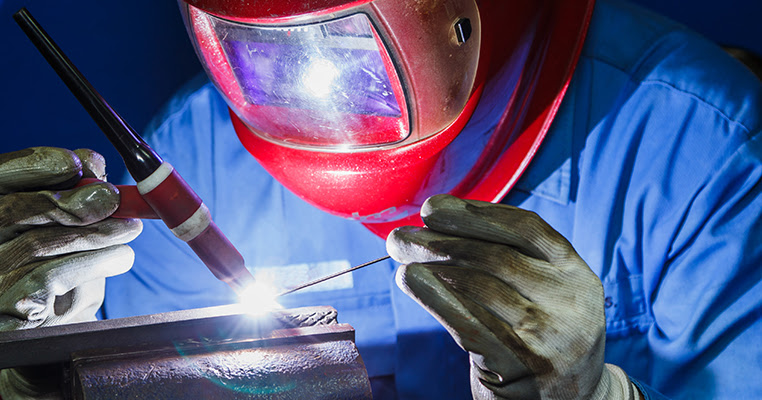
When titanium is heated enough to melt and fuse during welding, oxygen can enter the material and form titanium oxides. This causes the metal to become brittle and prone to cracking. Since titanium is generally used in high-stakes environments—where failure can result in the destruction of billion-dollar equipment or the loss of life—this is a significant issue.
How Do You Fight Oxygen Embrittlement?
Oxygen and other components of the atmosphere are well-known sources of contamination and damage when welding metals. We have tools and techniques to mitigate this risk, and we use them regularly. This is the purpose of a shielding gas: to replace the local atmosphere around the weld with something inert, like argon or helium, to protect the work area as it cools below the point where contaminants can affect it.
The problem with titanium, however, is two-fold.
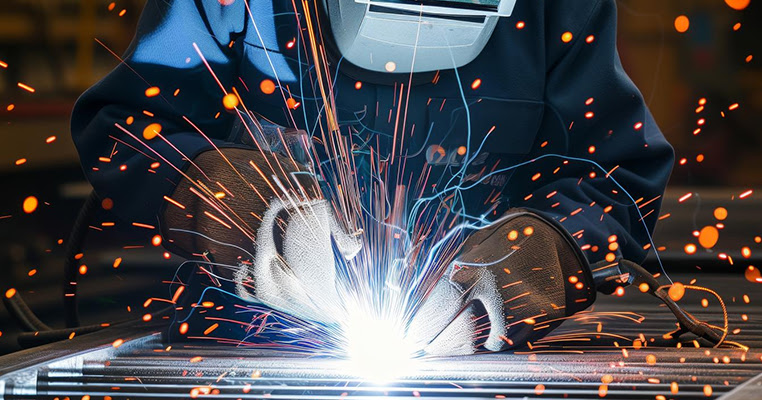
First, titanium is much more reactive than metals like iron, steel, or aluminum. While tiny amounts of oxygen might cause minor cosmetic issues with a steel weld, the same amount can devastate titanium. Shielding gas must be used extremely carefully to protect the welds from contamination.
Second, as mentioned, titanium is virtually impossible to “fix” once damage has occurred. If a weld goes wrong, the workpiece is essentially ruined. Given the high cost of titanium, a bad weld is a significant financial loss, and since titanium welding requires experience, it’s not something you can jump into without proper training.
Because of these factors, even though the process of welding titanium isn’t fundamentally different from welding steel, the margin for error—and the cost of failure—are so much higher that only the most experienced welders feel comfortable working with it.
How Can You Protect a Titanium Weld?
Protecting titanium during welding is primarily about ensuring that the metal never encounters oxygen during the process. Shielding gas like pure argon is essential, and the quality of the argon must be carefully controlled. Using a regular canister or an argon mix with impurities can lead to disaster.
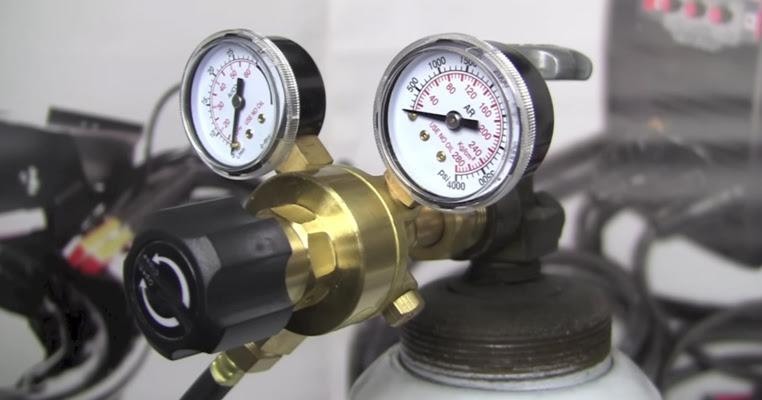
Additional tools can help as well. For instance, purge dams and trailing shields—specialized tools that most welders don’t typically need—are often essential for welding titanium. Learning how to use these tools can be time-consuming, and they add to the cost of consumables, making titanium welding even more expensive.
Perhaps one of the greatest challenges of titanium welding is simply having a steady hand. Even slight movements or jerks can misalign the weld, cause mistakes, or result in a bad weld and a ruined workpiece.
How Can You Tell if a Titanium Weld is Successful?
One of the advantages of welding titanium is that it’s usually immediately obvious if the weld has been done correctly.
When you weld titanium properly, the cooled metal will appear bright, silver, and shiny—just like it did before welding. That’s the natural state of titanium once it’s refined. It doesn’t require additional cleanup or coatings to look pristine.
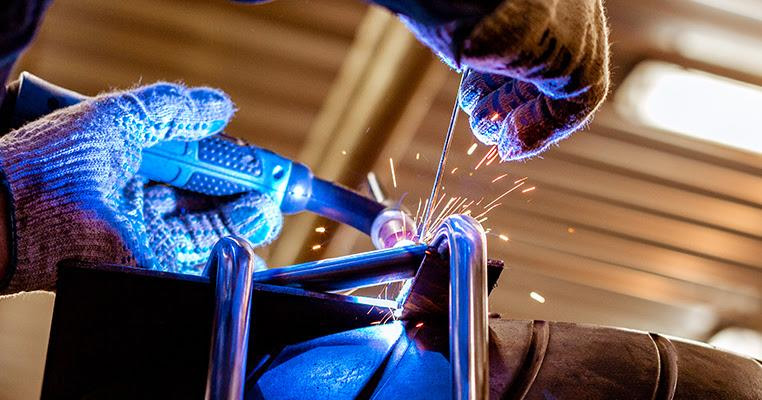
If oxygen or another element contaminates the weld and creates oxides, the metal will be discolored. The weld might turn blue, purple, or brown—clear signs that something went wrong. Experienced titanium welders can often tell at a glance if a weld is successful for this reason.
There’s also a color scale for the weld pool itself. When the molten titanium is light straw-colored, everything is fine. As the color progresses through dark straw, green, purple, blue, gray, and finally chalky white, the weld quality deteriorates. The further along the scale you go, the worse the weld.
The challenge here is that inexperienced welders, particularly those familiar with more forgiving metals like steel, may not immediately recognize how crucial color is in titanium welding. With steel, discoloration doesn’t necessarily affect the strength of the weld, but with titanium, color change is a warning sign that the weld might fail.
Are There Better Ways to Weld Titanium?
There certainly are better ways to weld titanium. Given that titanium requires welding in a pure argon environment and with steady hands, modern welding technology offers a solution: automated welding machines and CNC technology. These tools allow precise control over everything from torch movement to heat application and the composition of the atmosphere surrounding the workpiece.
However, there’s a significant difference between holding a welding torch and programming a CNC machine. Welding torches are cheaper and more accessible for many, and the skills required don’t directly transfer to CNC operation. Setting up and running a CNC welding system is an expensive and technical process.
Additionally, CNC systems are best suited for repetitive tasks. They’re less useful for spot repairs or individual welds, where human expertise and dexterity are still invaluable.
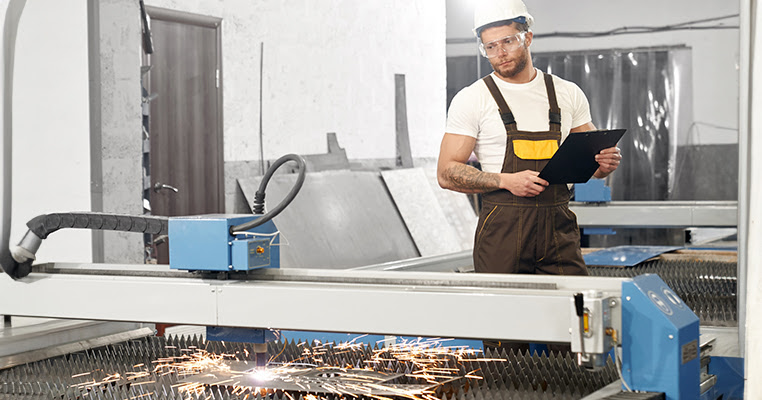
Is It Worth Learning to Weld Titanium?
While it’s a personal decision, the answer is likely yes. Despite the complexity and expense of titanium welding, there’s always a demand for skilled welders in this field.
The use of titanium is growing worldwide, and continued advancements in technology are making it more cost-effective to produce, which in turn makes it more accessible. While titanium welding has its challenges, it’s a lucrative skill to have in industries like aerospace, biomedical, and manufacturing.
Titanium welding offers the opportunity for a fulfilling career in high-stakes environments. While it may be difficult to master, the rewards are great for those who invest the time and effort to learn.
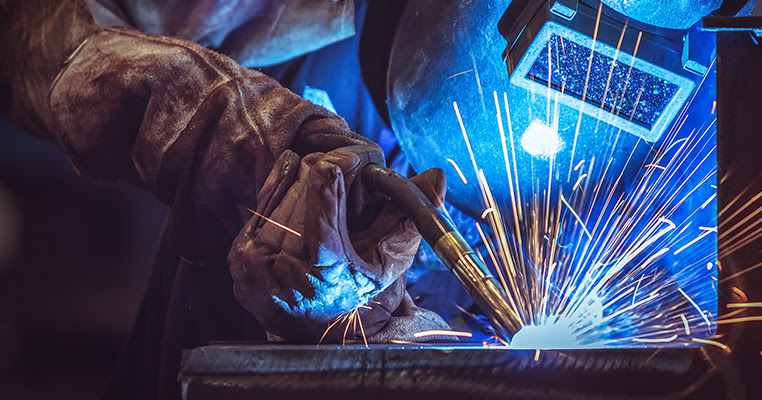
At Red-D-Arc, we work with welders of all levels, from individuals in small shops needing occasional welding to large fabrication facilities requiring advanced CNC and automated welding systems. Whether you’re working with standard iron or specialized titanium, we’re here to help. Reach out, and we can guide you to the resources you need to learn or help you select the right welding equipment to meet your needs. You can also explore more about titanium welding and other welding topics throughout our blog. We look forward to working with you!