April marks National Welding Month—a time to celebrate the critical role of welding and the skilled professionals who contribute to our industries and keep them moving forward. In recognition of National Welding Month, we interviewed Frank Carbone, one of Red-D-Arc’s talented Weld Automation Specialists, to discuss his dynamic 30-year career in this ever-evolving field. Frank’s journey from electrical engineering to welding technology and education showcases the innovation and expertise that make our industry what it is today. In this interview, he shares his insights on the evolution of welding, the growing demand for skilled welders, and why welding is such a rewarding career path.
Red-D-Arc: How did you get into the welding industry?
Frank Carbone: I was the Engineering Manager for a company called Ericson Manufacturing (in the Cleveland, Ohio area). One of the products I designed there was GFCIs. We tried to sell our GFCIs to Lincoln Electric for their engine-driven welders, and we were thinking of a proprietary GFCI for them specifically for their engine-driven welders. They ended up not buying it from us and just continued to buy the “off-the-shelf” GFCIs like their competition does, but I made contacts there during our meetings.
I later heard that Lincoln Electric was hiring for their Engineering Department, so I applied. Lincoln Electric is one of the premier employers in Cleveland, so this was a great opportunity, but I knew nothing about welding, just electronics. They hired me and sent me directly to the Engine Drive R&D Group (probably because of my previous meetings with that department). I didn’t design a GFCI for them; however, they put me on the “Chopper Technology” project. There was only one person working on it (Ivan Baker) at the time. We, together, were able to get a working prototype put together, in short order, and it became one of the top engineering projects in the company.
My background was electrical engineering, however, not welding, so they sent me to the Lincoln Electric Welding School. I attended a few hours a day while I was at work, and did this for several months until I completed it.
After several years in Engineering at Lincoln Electric in Cleveland, I heard they had an opening in Arizona (my favorite place) for a Factory Rep. So I applied for it and got it. I later left Lincoln Electric and taught welding for two years before coming to Red-D-Arc. I started at Red-D-Arc as an Account Manager and, about nine years ago, became a Weld Automation Specialist. I’ve been in this industry for about 30 years. I’ve been with Red-D-Arc for 14 years.
One of my favorite things to do at Red-D-Arc is to train new Account Managers and others in basic welding and the Red-D-Arc product line to improve their sales abilities. I have done several training seminars at Red-D-Arc with great success in all of them.
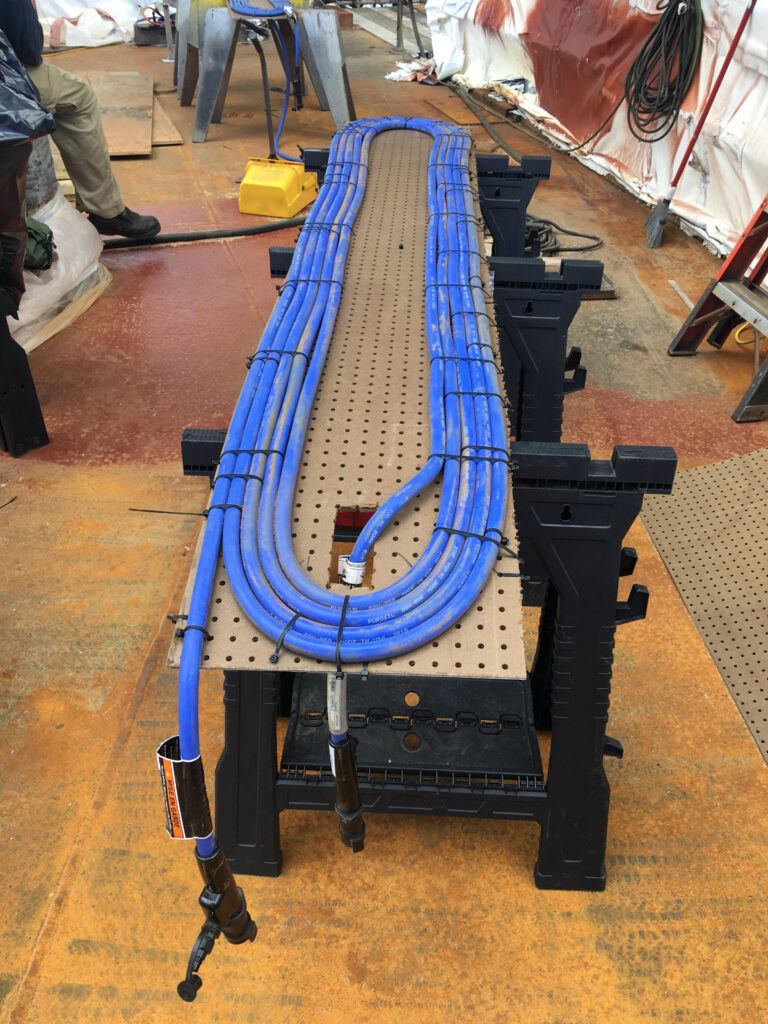
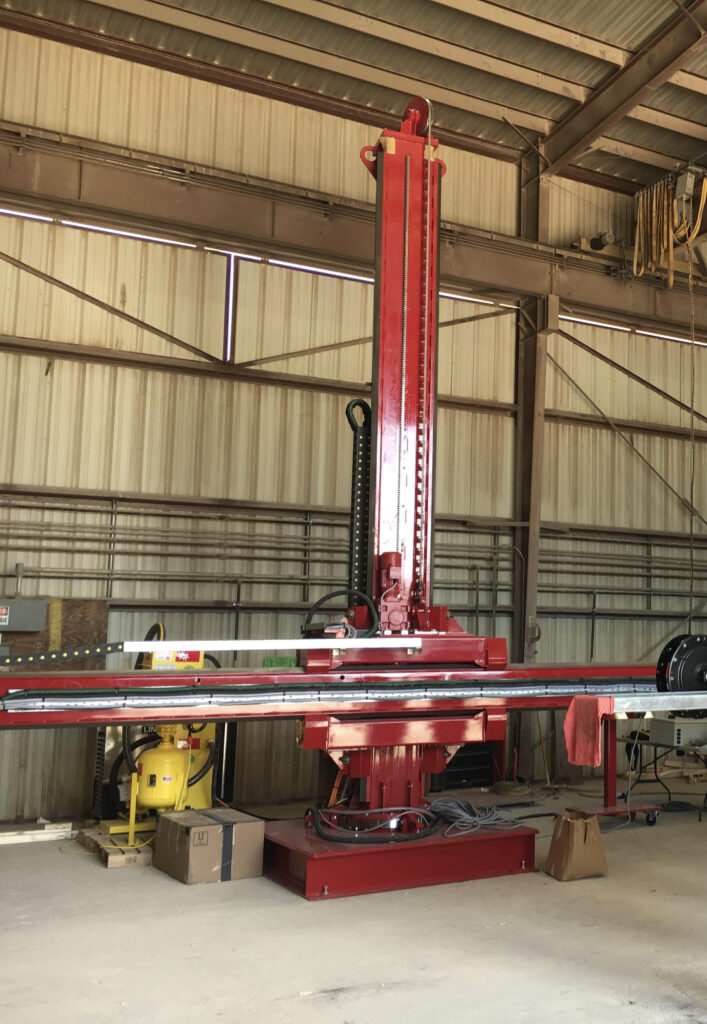
RDA: What certifications/training do you have?
FC: I never worked in the industry as a welder who was welding everyday so I don’t hold any specific welding certifications. I am a Technical Community Leader (TCL)* and was among the first three Red-D-Arc people to hold this accomplishment. But when I taught welding, I specialized in teaching GMAW, FCAW-S & FCAW-G.
I know all the welding processes, however, as I designed welders that can operate in all phases of welding, all the processes. While at Lincoln Electric, besides designing the “Chopper Technology” (which is still used in their welders today), I designed the “Touch-start TIG” starting system, which is still used in most of Lincoln’s inverter welders today. I designed the R305G (and D)—the R305G is also known as Red-D-Arc’s GX300, which Red-D-Arc has had in their fleet for two decades or so. The GX300 is Red-D-Arc’s version of the R305G.
*A Technical Community Leader (TCL) supports and guides a community of welders by sharing expertise, promoting best practices, and fostering collaboration. They lead initiatives such as training sessions, forums, and workshops to help welders grow their skills and stay aligned with industry standards.
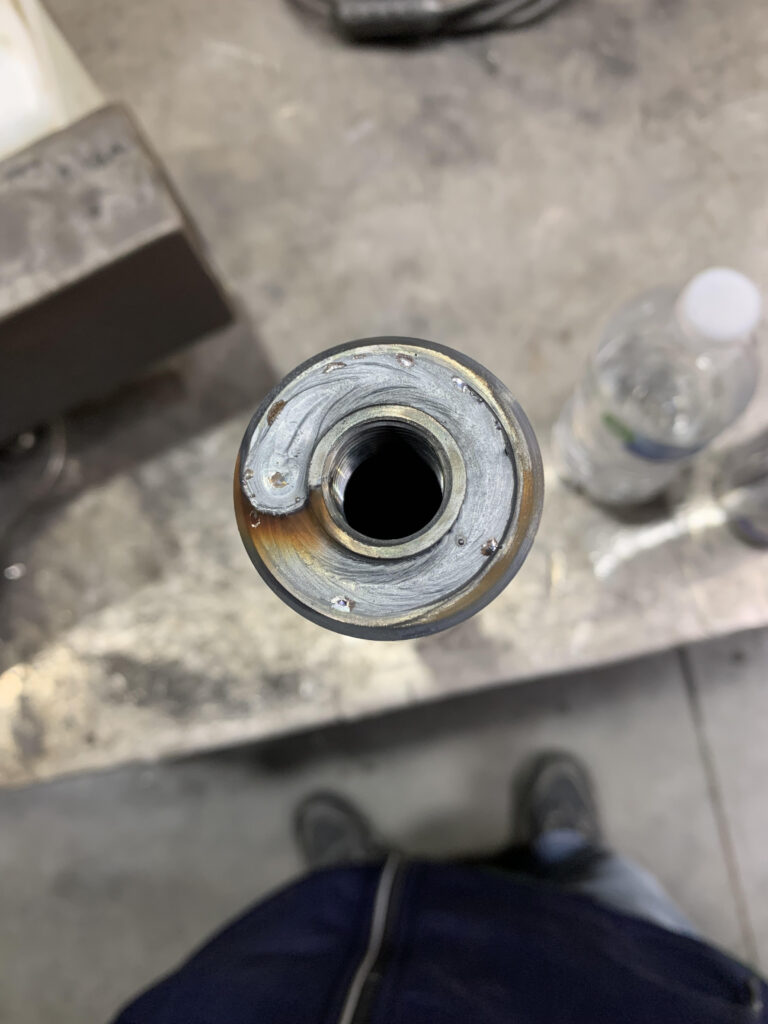

RDA: What do you love about welding?
FC: A lot of my welding experience has been as a designer of welders and a welding instructor. I love teaching people how to weld and seeing “their eyes light up” when they succeed. I am even still in touch with some of my former students via Facebook today. I also love troubleshooting people’s issues and seeing the success in those situations.
RDA: What’s your most memorable welding moment?
FC: In general, coming to customers with an issue(s), explaining to them what I “think” might be their problem (they sometimes initially disagree), and then seeing their expressions when I correct what’s wrong… that’s “priceless”!
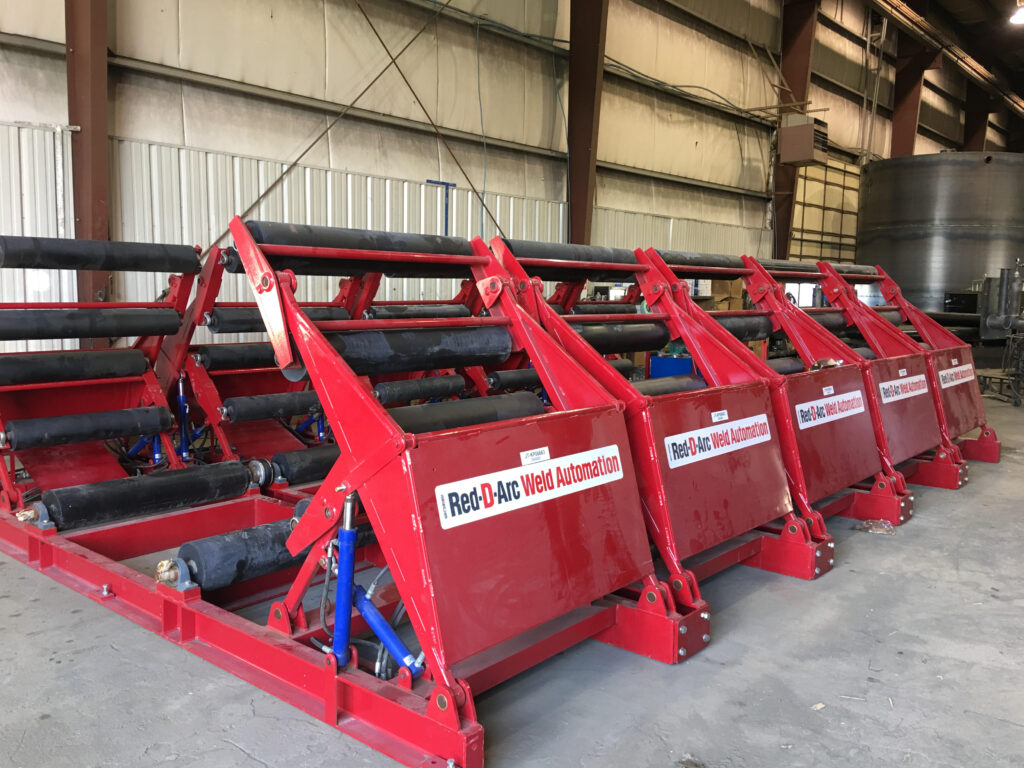
RDA: Share a welding fun fact.
FC: Improper grounding* is probably the issue about 80% of the time when a customer calls and says, “Your welder I’m renting doesn’t work”.
*In welding, grounding provides a safe path for electrical current to return to its source, minimizing shock hazards and ensuring proper weld quality. It involves connecting the metal components of the welding machine and workpiece to the earth, creating a low-resistance path for electrical current to flow safely.
RDA: How has welding technology changed since you started?
FC: Computers… that is what’s changed. Welders have become more and more computerized (and smaller with the advent of inverters) since I started in this industry back in the mid-’90s. When I started, Lincoln Electric had tried to use computers in engine-driven welders, with limited success.
They did have success in their Power Wave System with computers, though, and that success has continued in this product line but has spread into other models of welders. High-tech welder success has become more and more prevalent in a large number of welders by all manufacturers. Miller and ESAB have both done a lot to advance high-tech in the welding industry.
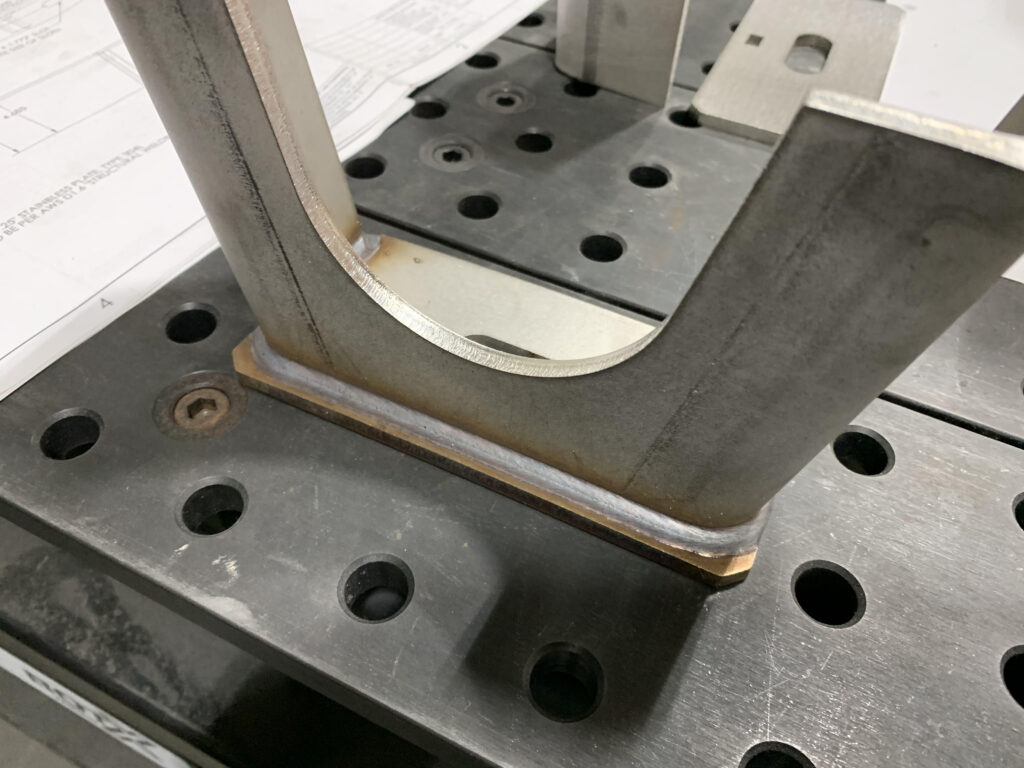
RDA: What advice do you have for the next generation of welders?
FC: There is a large deficit of welders in this industry. Previous generations have retired, changed jobs, and even passed away, and thousands of their positions have never been replaced. A good welder can have a great career and be paid well. Many upcoming people do not want the job because it’s “hot,” “dirty,” and “physical.” If a person can get past those perceived “negatives,” they can have a great lifelong career.
RDA: Why would you encourage young people to choose welding as a career path?
FC: Because, as stated above, the need is there. It is also a fulfilling career when a welder sees a building or any product they welded in existence and they can say, “I did that!” I do that when I see a welder I designed on the back of a truck going down the road. Welding is also a form of art. A good welder can make some of the most “artistic-looking” welds and again say, “I did that!” It is a fulfilling job.
As we continue to celebrate National Welding Month, Frank’s career journey helps us appreciate the vital role that welding plays in shaping our world. From advancing welding technology to helping build the next generation, his passion for the industry is evident. With the growing demand for skilled welders, there has never been a better time to explore a career in welding. Thank you, Frank, for sharing your insights and expertise, and helping to inspire the exciting future of welding!
Leave a Reply