Welding is an essential task for many shops, from workshops that need occasional welding, to facilities that weld as part of operations every day, to fabrication facilities doing nothing but welding.
Regardless of how much welding you need to do, it’s critical – absolutely essential – that your shop has a space set up properly for welding safely. Welding presents many risks, including:
- High currents of electricity that present an electrocution hazard.
- High heat that can be a burn hazard.
- Sparks that can be both a burn and fire hazard.
- Bright lights that can be a hazard to vision.
- Loud noises that can be a hazard to hearing.
- Fumes that can be a respiratory hazard.
While all of these hazards can be mitigated, it’s important to make sure to actually do so. Lax safety is the leading cause of workplace accidents, and when you’re dealing with the kinds of risks a welder presents, that can have serious long-term consequences.
So, how do you set up a space to weld safely? Let’s talk about it.
Consider a Separate Space
Sometimes, your welding needs are sporadic and don’t warrant setting up a dedicated space for it. In these cases, you’ll want to take as many steps and precautions as possible to ensure the safety of your welding operator and anyone else in the space, as well as the space itself.
It’s usually better, though, to have a dedicated space for welding. Many of the best ways to handle the hazards involved with welding require that you outfit a space with safety equipment, and that’s easiest to do if you don’t need to move it out of the way of other operations.
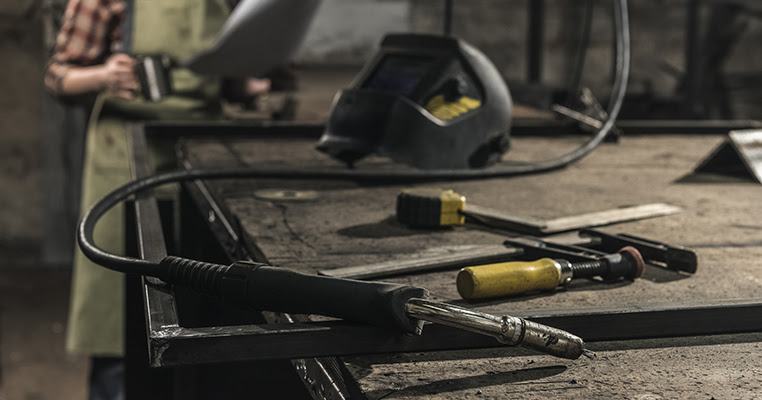
So, carefully consider how much welding you’ll be doing, and if possible, consider a dedicated space for welding. We’ll be writing the rest of this post as if you’re setting up such a space, but many of our tips can work equally in both situations, so make sure to read through.
Either way, make sure that you have enough space for your welding operators to work comfortably. A cramped environment increases stress, fatigue, and danger, so you need space for the people, projects, equipment, and storage necessary for the smooth operation of your welding.
Check the Floor
Sparks, spatter, and debris can fly as far as 40 feet away from a welder in operation. That means for proper safety, you need to consider everything that will be within that area. What better place to start than the foundation itself?
Ideally, your welding area should have a solid cement floor. That way, nothing is at risk of burning from a stray spark or glob of molten metal. It’s also non-conductive, which eliminates the risk of metal flooring. A packed dirt floor can also work, though you’ll have more issues with dirt and dust in your shop in that case.
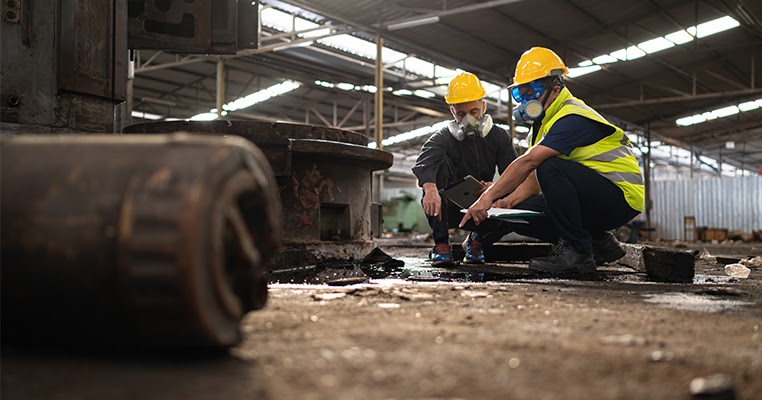
You also want to check the floor for tripping hazards. Hoses and cables are necessary for welding – you need electricity and gas, after all – but you want as little as possible trailing across the floor, both during operation and when the equipment is put away. There are many solutions to this, including ceiling drops, but it’s a consideration that must be made.
Strong Lighting
You need to see what you’re doing when you’re welding. This is difficult because welding generates an extremely bright arc of electricity, so you need eye protection that darkens to protect your eyes from that glare.
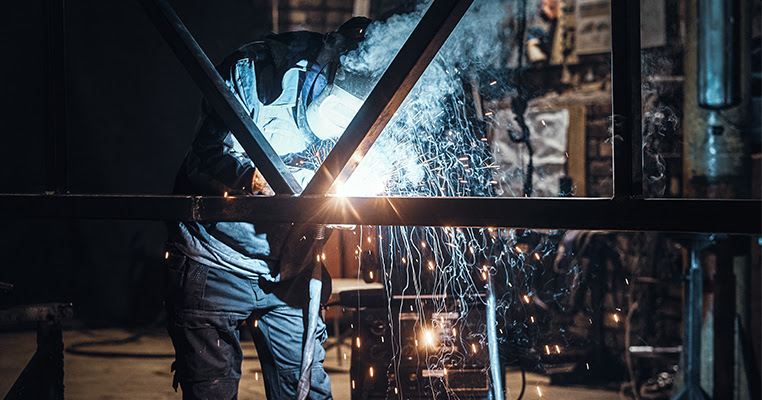
So, you need lighting for your workspace that is bright enough to illuminate your working area even when you have a welding mask on. Ideally, this shouldn’t be your sole source of light in the area, either; more gentle light for when your mask isn’t on is also necessary.
Good Work Surface
Where are you doing your welding? Not just in what area of your shop, but where specifically? Sometimes, you don’t have much of a choice – an auto repair shop might need to work in tight spaces to fix the frame of a vehicle – but if welding on mobile workpieces is the way you work, having a dedicated workspace is a great idea.
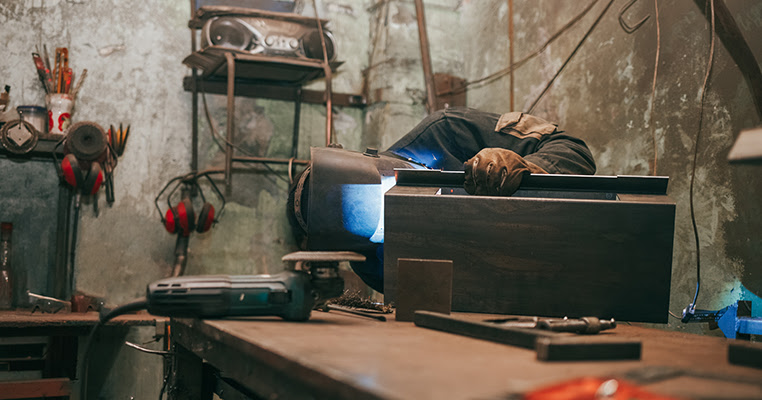
One great option is a welding table or positioner. There are a variety of mechanisms that serve this function. Some are essentially workbenches with built-in fume extraction. Others have rotary and rotational settings to move and position your workpieces at any angle you need them. Otherwise, simply having a fire-resistant workbench may be all you need.
Separation from the Rest of the Shop
Many of the hazards of welding can travel. Specifically, the sound, the glare, and the fumes, as well as spatter and sparks, can all travel quite some ways from the actual welding operator and their workpieces.
Ideally, you will have your welding area separated from the rest of your shop with walls, a door, or some other barrier. This protects others who walk by from catching the glare – which can damage eyesight very quickly – and from breathing in welding fumes.
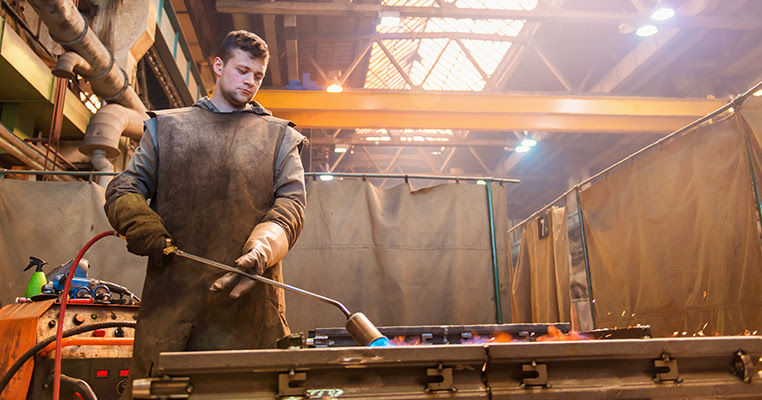
If you can’t dedicate a segmented space to welding, at least have barriers you can put up around the working area. Welding curtains, for example, can be drawn to segment an area both physically and visually while still being able to be moved through and pushed out of the way when more open space is needed.
Ventilation and Fume Extraction
Welding fumes can be extremely hazardous to the health of your welding operators and anyone else who shares the space with active welding. Proper ventilation and/or fume extraction systems are required for safe welding.
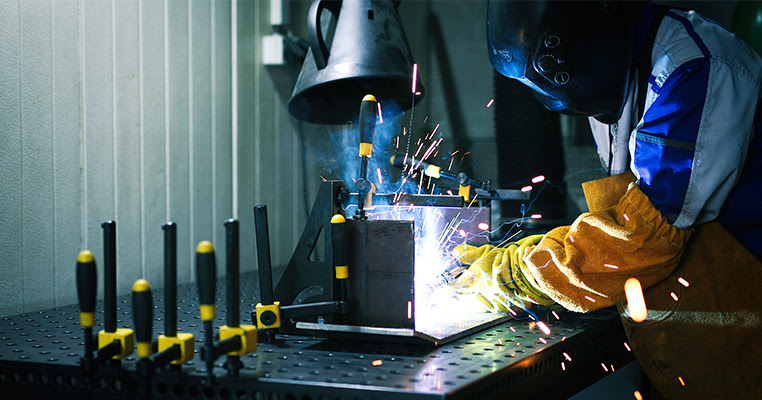
Your two options are stationary fume extraction systems and portable fume extractors. Portable units are smaller and can be positioned close to an active job and recirculate air in their space after passing it through a filter. Stationary systems are typically capable of circulating all of the air in a space and venting it outside, though some may have directed hoses for more guided suction directly above a project.
You can read our full breakdown of portable and stationary fume extractors here. We also offer a range of fume extraction systems of both types in our rental equipment catalog.
Proper Storage
Another element of a good welding area is proper storage for the items and materials you need in your operations. Make sure any storage containers you use are fire-resistant or fireproof and that they can safely hold the kinds of items you need.
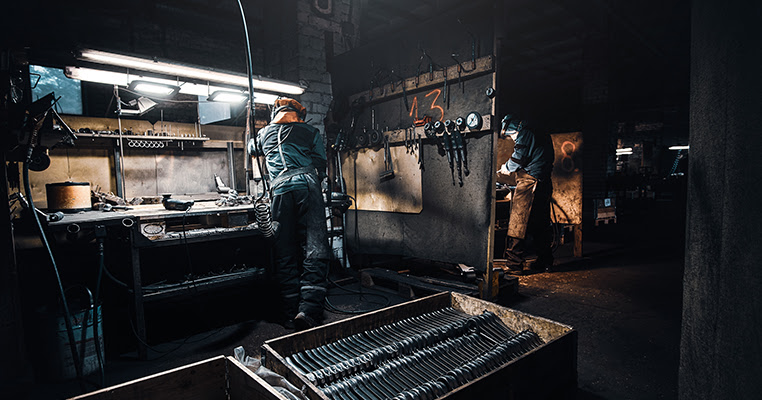
Consider space for:
- Welding machines themselves. These take up a decent amount of space and need to be put somewhere while they aren’t in use. Since your workshop may need more than one kind of welding machine, you need to either consider a multi-function machine (which will be larger and more expensive) or several individual machines with dedicated functions.
- Consumables. All of your spare nozzles, electrodes, welding filler rods and wires, and all the rest need to be stored somewhere convenient. If you need to send someone clear across the building for a filler rod in the middle of a project, you’re losing a lot of productive time.
- Gas cylinders. Welding generally requires a shielding gas, and those gas cylinders are a hazard themselves. They need to be stored properly, upright, labeled, and away from other hazardous gasses so there can be no risk of mix-ups.
- PPE. Welding helmets and masks, protective jackets, eye protection, gloves, hearing protection, and anything else necessary to keep your welding operators safe needs to have a place nearby that they can be stored so there’s not even the flimsiest excuse to “do without just this once.”
Remember that all of these storage containers, racks, and other furniture will require space in your welding area.
Safety Equipment
One of the most important things to have on hand is, as mentioned above, PPE. Personal protective equipment is required for safe and effective welding.
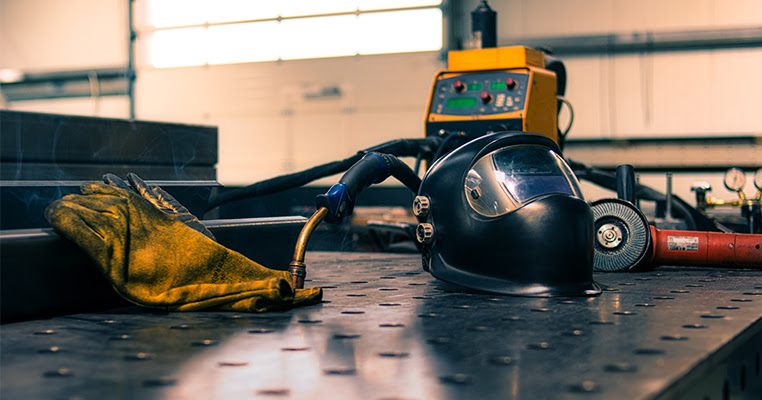
If you don’t have the right PPE on hand, you shouldn’t be welding at all.
- A welding helmet. Welding helmets are critical for both spark/fire/spatter protection and eye protection against the blinding light of an electric arc. Your operators need helmets that fit and properly protect their eyes from the glare.
- Protective clothing. There are several pieces here, including welding jackets, aprons, gloves, and more. The exact combination can vary and may be part of your operator’s wardrobe rather than in-facility equipment, but you should always have something on hand as a backup, just in case.
- Respirators. A good respirator serves as a backup to ensure that even small amounts of toxic or noxious fumes escape your fume extraction system.
In addition to PPE, your welding area needs the right kind of gear and equipment on hand to handle any emergencies that can arise in operations.
A fire blanket is a good emergency item to keep on hand in the case of a fire. Similarly, fire extinguishers rated to extinguish any sort of fire that can arise in the area are also important to have on hand and accessible. Since some metals can be ignited and difficult to put out, this may need special consideration.
Part of PPE is protecting your operators from the risk of burns, but it’s also a good idea to have first aid on hand that can handle burns if they happen.
Accessories and Secondary Tools
There’s an immense number of possible items that may be useful or necessary for proper welding, depending on the kind of welding you’re doing.
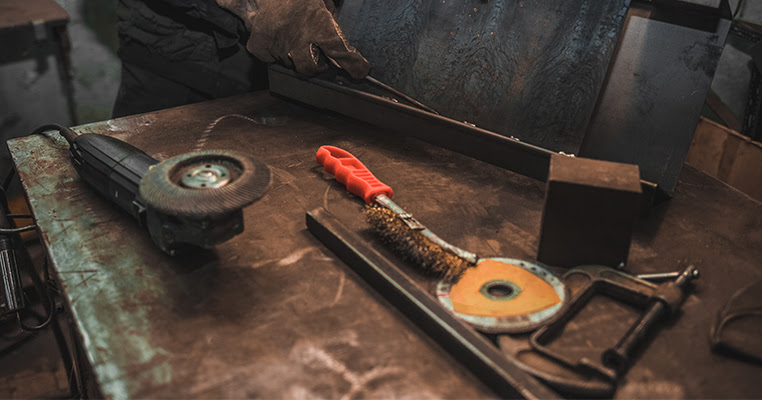
For example:
- Metal saws, like band saws and chop saws, are used to cut pieces to size.
- Pliers, vice grips, clamps, and pry bars are all useful tools to have on hand.
- Grinders can be important for fixing mistakes and removing minor excesses in a material.
- Wire brushes and other mechanical cleaning devices are important for cleaning materials before welding them.
This just scratches the surface of the array of tools and other items you might need to keep on hand or available when welding. The specifics will depend on what you plan on doing in your shop when welding is involved, what else your shop is already doing, and what capabilities you need on hand. Don’t worry about getting this one perfect out of the gate; establishing the right array of tools is more of an ongoing process than it is a destination.
The CNC Option
Many – though not all – of the considerations above can be handled in just one package: a self-enclosed CNC machine. CNC machines enclose the workpiece in a shielded and fume-extracted workspace, use precise computerized movements to guarantee appropriate welds, and keep the operator out of harm’s way.
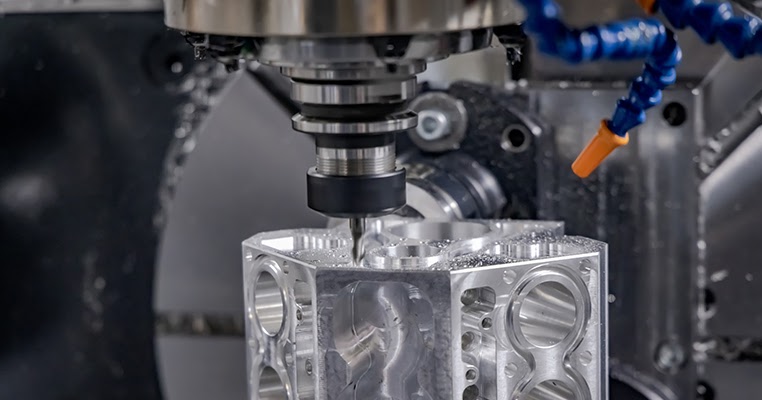
There are a few problems with CNC machines. The most obvious is the expense; a large-scale CNC machine can be very costly. They also tend to be bulky and heavy, so it can be difficult to find the right space for them. They also dramatically change the workflow, requiring more CAD and computer skills out of your operators than welding experience. They are also best used for repeatable projects, rather than one-off welding needs, so that may or may not fit with your use case.
A CNC can be an excellent option if it suits your needs, but it might also be an expensive device that doesn’t cut it. It’s an evaluation you’ll need to make for yourself.
The Ideal Equipment
The key to any good welding facility is the welders themselves. Whether you need a MIG, TIG, or another process or multi-process machine, something powered by gas or hard-wired, something with advanced computerized capabilities, or just the simplest equipment, there’s something out there for you. The trouble is finding it.
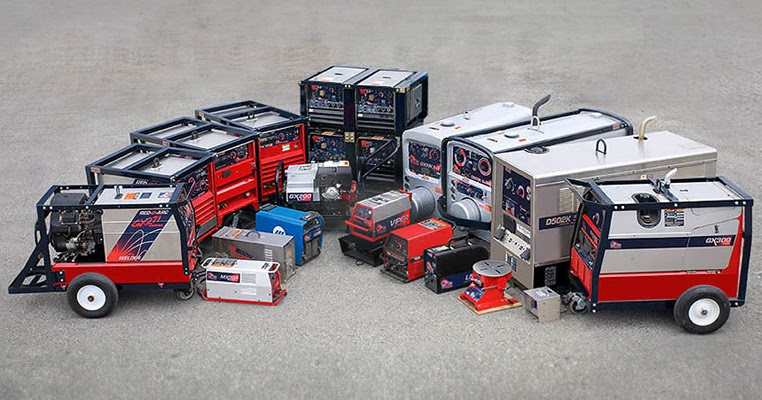
That’s where we come in. At Red-D-Arc, our rental welding equipment covers all the bases. Once you have a basic idea of what capabilities you need, you can find machines that suit your needs and rent them to try them out. If you like them, great!
Keep the rental going, or buy one for yourself, either used from our store or new from the vendor. Or, if the machine doesn’t quite work the way you need it to, return it and try another with no significant loss. If you don’t know what you need, you can also contact us, and our experts will be happy to help you decide.