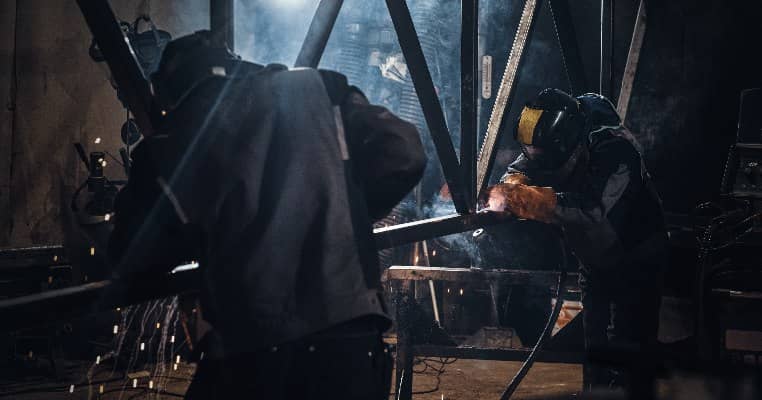
Prefabrication in the construction industry is likely to remain an ongoing trend. The skilled labor shortage, growing demand, and tighter margins increase the need to create the construction elements in a controlled environment.
Why is the controlled environment so important? Well, the key lies in absolute management and leaving very little to chance and environmental factors.
When elements of buildings, infrastructure, and industrial facilities are produced serially, process control and project cost efficiency increase significantly.
Let’s First Define Prefabrication
Prefabrication is the act of making building/infrastructure components in another location off-site. Once completed, prefabricated elements are transpired to the project site. Next, they are assembled, and the building or other project is delivered to the client.
Prefabrication can refer to manufacturing building pieces, like walls and floors, and assembling them on-site or manufacturing whole units comprised of walls, floors, windows, and other elements. So, there are various approaches and degrees to prefabrication. This is also the case when observing the prefabrication of pipelines, bridges, and other infrastructural projects.
“Different applications come with their own sets of problems that can benefit from welded prefabricated elements/assemblies”
Prefabrication Applications In Construction
While prefabrication in construction mainly refers to the prefabricated construction of homes, buildings, and industrial facilities, nearly everything else can be prefabricated.
Some of the best examples of how diverse prefabrication use can be are:
- Residential buildings and individual homes.
- Commercial buildings like warehouses and offices.
- Industrial facilities like mills, petrochemical plants, power generation stations, manufacturing plants, and many others.
- Docks and marine bays.
- Carports and other elements of parking lots.
- Farm buildings and equipment like silos.
- Greenhouses.
- Garages, large and small.
- Ramps.
- Piping systems.
- Infrastructure like bridges and dams.
- Power line transmission towers.
- Airplane hangars.
There are many other less obvious applications of prefabrication in construction that aren’t just solely meant for buildings. While the word prefabrication usually implies application for building construction, prefabrication is used all around us. So, if you offer prefabrication services or plan to venture into this business, you can consider a broader market and find prospects others might have overlooked.
Why Should You Consider Prefabrication
If you were a contractor working on a high-rise commercial building in the city center, you would have a tough time constructing the building without any prefabrication. The dense urban vehicular and pedestrian traffic would make material delivery challenging. Not to mention the increased risk of worker injury when fabricating everything on the spot tens of stories high.
Likewise, working on a commercial building or a piece of infrastructure in a rural area brings its share of problems. First, you would waste much time and resources on material delivery as the suppliers are likely not local. Next, you’d struggle to find enough skilled workers who’d want to be relocated and spend a long time working on the project in a remote area. This issue is easier to solve if you prefabricate the parts and assemble them on-site. Less time is spent in the remote location, making it easier to handle labor-wise.
The list below can give you the most important reasons to consider prefabrication. But, depending on the job, you could benefit from prefabrication in other ways too.
- Mitigating the labor shortage – Applying skilled labor in a focused, controlled environment of the manufacturing line or shop floor provides a significant productivity gain. In contrast, fabricating everything on the construction site requires more effort and time, making it more challenging to achieve your goals with the global skilled labor shortage affecting everyone today.
- Higher efficiency – Construction sites are weather-dependent, messy, and complex to organize. Working in an indoor shop that’s organized for efficient production drastically speeds up the process.
- Reduced costs – Faster time-to-completion and more efficient material use saves resources on two fronts. First, you get to complete more projects in a calendar year, meaning that your labor force provides a higher ROI on their costs. And second, less material is wasted in a controlled production environment, allowing for additional savings. Finally, you don’t need to allocate as many resources for material transport.
- Improved quality control – Shop prefabrication allows for strict quality control at each step of the production. Furthermore, leaving only the assembly step for the on-site fabrication reduces the chances of a construction defect going unnoticed.
- Enhanced sustainability – Prefabrication has a lower environmental impact than on-site construction. Less material is wasted, it’s easier to avoid disruption of the local environment, it saves water, reduces the need for using diesel-powered generators, and cuts the energy cost of material and personnel transport.
- Better work safety – Following safety codes and standards in the shop is much easier than on-site. Once the prefabricated elements are brought on-site for assembly, fewer safety hazards can affect the workers. Also, the site is less crowded, and there is less material that can present a hazard. Since the process is streamlined, the unpredictability factor of the on-site job is reduced when working with prefabricated elements.
Welding And Prefabrication In Construction
Welding is the backbone of the construction industry. This doesn’t just include high-rise buildings but infrastructure and the industrial sector. Every welding process is used in construction projects, from heavy-duty submerged arc welding (SAW) to light short-circuit MIG welding. Almost every material is used in the construction industry, except exotics too costly for real-world applications.
When it comes to metals, structural steel dominates the construction industry. But, aluminum, stainless steel, low and high-alloyed steel, titanium, and nickel alloys all need to be welded for various applications.
Since the construction industry is so diverse, it includes everything from I-beams to specialized pipelines and petrochemical reactors. All of which require a different welding approach and following specialized welding codes and standards. Likewise, different applications come with their own sets of problems that can benefit from welded prefabricated elements/assemblies.
Building Construction
Building residential and commercial buildings requires a lot of welding, especially in the commercial sector. These welding jobs primarily focus on structural welding, like H and I-beams, trusses, piles, columns, footers, walls, decks, roofs, and other structural elements of the building.
Prefabricating individual elements, like walls or whole room assemblies, can significantly improve construction speed, cut costs, and improve workplace safety. Likewise, prefabricating structural elements like trusses and beams and delivering them on-site saves a lot of resources compared to welding them on-site.
For example, you can use welding manipulators in combination with a submerged arc welding system to fabricate structural components quickly and with consistent production quality. Likewise, a self-propelled mechanized sub-arc tractor is an excellent choice for long welds in the flat and horizontal position, like fillets connecting a web and a flange in an I-beam.
Our welder rentals include everything from stick to MIG, TIG, and stud welders, which are indispensable for welding prefabricated building components. Using our welding power sources with weld automation systems for modular building construction gives you a significantly higher level of quality control. It also makes it easier to achieve AWS D1.1, D1.2, D1.6, and other structural welding standards.
Infrastructure Projects
Bridges, dams, water systems, waste management, railways, and other critical infrastructure construction projects also benefit from welded prefabricated elements.
Structural welding is the most critical part of infrastructure projects. But pipe welding also plays an important role in water systems.
SAW is the primary welding process used for megastructures like bridges. But, flux-cored arc welding (FCAW) is also widely adopted for welding thinner elements with high productivity.
It’s much more efficient to manufacture massive structural steel elements and bring them on-site for assembly. Welding in bridge building is all about shop welding and on-site assembly. While it’s sometimes necessary to weld these elements together on-site, prefabrication significantly reduces the time to completion and worker exposure to dangerous high-elevation tasks.
Industrial Sector
The industrial sector is the most diverse part of the construction industry. It encompasses everything from mills, power generation plants, and manufacturing plants to oil refineries and offshore structures. Of course, every welding process and its variations are applied here, including highly specialized processes.
While industrial facilities require SAW and FCAW for structural elements, there is a massive need for MIG and TIG welding for specialized equipment and pipes and tubes.
A typical industrial facility can have numerous ASME pressure vessels, heat exchangers, process piping systems, and storage tanks. Each of these can be made from various alloys, thicknesses, and shapes, requiring a highly diverse set of skills and welding equipment to produce them productively.
That’s why prefabrication is critical for industrial construction. If you weld a pressure vessel, it’s much more efficient to do it in-house than on-site. Sometimes, that may not be possible, but most of the time, it’s what customers and contractors do. Even massive petrochemical reactors that weigh hundreds of tons are prefabricated and delivered on-site.
Pipe welding equipment, like pipe bevelers and cutters, orbital welders, and pipe rollers, are critical for producing high-quality joints. Likewise, using an indoor solution, like the Miller PipeWorx Welding System, allows you to prefabricate piping systems much faster. Miller’s Regulated Metal Deposition (RMD) is a phenomenal MIG welding technology that achieves exceptional root welds when welding pipe and can even eliminate the need for a purging gas for some stainless steel jobs. This makes the fabrication process much faster and significantly less costly.
Managing a large pressure vessel can be very challenging, time-consuming, and dangerous. However, using welding turning rolls and fit-up bed rollers makes rotating the vessel and fitting the joint a breeze.
Welding process pipes, flanges, valves, manholes, manifolds, and other specialized equipment can also require using a TIG power source. Our TIG welder rentals include the Miller Synchrowave and Dynasty machines, which can weld almost every alloy that can be arc-welded.
Prefabricating industrial equipment not only saves resources but makes weld inspection and quality assurance much more effective. Industrial equipment often requires welding with a shielding gas, which cannot be 100% reliable if done outside. Likewise, conducting NDT inspection in a predictable environment of your shop will let you spot any defects in time.
How Cobots Can Boost The Prefabrication Productivity
Arguably, cobots are the most impactful technology to have hit the welding industry in recent times. A welding cobot can drastically boost shop’s productivity and weld quality when working with small to medium-sized part batches.
Prefabrication and cobots go hand in hand. While industrial robots are better suited for massive quantities of parts (1000+ pcs. per batch), the vast majority of construction jobs where prefabrication can be used require smaller batches (50-250).
For example, welding a steel frame for a prefabricated wall could be automated with two or more cobots, depending on the size. You could position the cobots in two diagonal corners of the work table and program them to weld the frame components. Once they do the welds, the operator unloads the frame and loads the new elements in the fixture.
The same can be applied to many repetitive welding tasks in the construction industry. Brackets, flanges, stiffeners, custom parts, you name it. If it has a relatively simple geometry and you need it in small to medium-sized batches, you can almost always automate the welding process with a cobot.
You can even work with complex geometries after you gain some experience. Cobots have cut production time in half for many fabricators, drastically boosted productivity, and helped many solve the skilled welder shortage. So, if they aren’t already, cobots should be in your crossheads as a technology to learn about and implement in your workflow.
The cobot advantage is that anybody can learn how to use them in hours, not days. They are not made for programmers like traditional industrial robots, but for welders and metalworkers.
Red-D-Arc BotX Cobot is so simple to use that non-welders, and even non-tradespeople, for that matter, can run their first weld in less than an hour from the first time they use it. All it takes to program it is manually guiding the BotX’s hand to show it the path and using the intuitive app to adjust the weld settings.
Rent or Lease From Red-D-Arc
No matter your position in the construction industry, we have the equipment you need for welding prefabrication. Contact us today, and our team will help you find the most suitable equipment for your next job. Buying large weld automation systems, high-end welding power sources, and cobots is not always cost-effective. Renting from Red-D-Arc can give you an immediate ROI for the job at hand and help you bid on previously inaccessible projects. Don’t skip on the power of weld automation and the advantage of renting the equipment. Many fabricators struggle to scale and can’t compete for larger jobs. Renting the right gear can help you immediately access technologies that can transform the way you fabricate and help you get to the next level.