Applications and Advantages in Tank Fabrication and Maintenance
In the fabrication of storage tanks, as in most other welding applications, there are two crucial processes that storage tank fabricators must carry out to ensure the final quality and durability of the tanks. They are weld preheating and post-weld heat treatment.
Pre-Heating
Preheating involves heating the material to be welded to a particular temperature before welding. This process reduces shrinkage by minimizing the temperature between the arc and the base material. It also removes moisture, lowers hydrogen, and slows the weld cooling rate. These reduce the risk of cracking, brittle welds, and failure of the welds. Preheating is crucial for storage tanks as they are to withstand high pressures during operation.
Post-Weld Heat Treatment
Post-weld heat treatment is carried out after welding, and has two major applications; stress relieving and bake out. During welding, ambient hydrogen may permeate the material, leading to hydrogen-induced cracking later on. Other volatile compounds that can later contaminate the components of the storage tank may also penetrate the material. Bake out is carried out by heating the fabricated tank to a specific temperature and holding it at this temperature for a specific period. This process allows hydrogen and other volatile compounds to diffuse out of the material. Bake out is usually carried out immediately after welding before the material cools.
Stress Relief
In stress relieving, on the other hand, the welded tank is first allowed to cool. It is then heated to a specific high temperature, held at this temperature for a particular period, and gradually cooled at a controlled rate. Stress relieving is carried out to relieve problematic stresses that might have built up during welding.
These heating processes are crucial in the fabrication of storage tanks. So the overall success and cost-effectiveness of your storage tank fabrication project largely depend on the efficiency, speed, and precision of the heating system used. There are various heating systems that you can use for your heating applications, such as resistance heating, open flame rosebud, and furnaces. However, induction heating systems provide maximum efficiency, accuracy, speed, control, and cost savings.
How Induction Heating Works
Induction heating is a non-contact heating method that heats metal parts by inducing currents in the workpiece. Hence the term “induction” heating. In induction heating systems, alternating current flows through a conductor, creating an alternating magnetic field. The workpiece to be heated is exposed to the alternating magnetic field, creating localized eddy currents in the metal workpiece. The metal’s inherent electrical resistance to the flow of current resists the eddy current, causing the workpiece to heat up. Furthermore, a phenomenon called hysteresis, which is caused by the metal’s resistance to the magnetic field, also contributes to the heating up of the workpiece, albeit to a much smaller extent.
This process, unlike resistance and open flame heating, doesn’t require any external heating elements. Instead, the part generates the heat itself from within. Simply put, instead of heating the part, induction heating causes a part to heat up in response to the application of and electric current. Induction heating systems typically consist of a power source/control which supplies the alternating current and provides digital control and copper coil cables, which are the conductors that are placed on or around the workpiece. Insulating material prevents contact between the conductors and the workpiece.
Benefits of Induction Heating
Induction heating systems are the best option for all your storage tank heating applications. They can be used in weld preheating, post-weld heat treatment, stress-relieving, and hydrogen bake out. Some of the outstanding benefits of induction heating are as follows.
Uniformity of Heating
Induction heating creates uniform and even heating throughout the workpiece. At no point in time during heating is one portion of the area undergoing heating at a higher temperature than another. This is because every part of the workpiece in contact with the induction heating system generates heat simultaneously.
In comparison, resistant heating pads heat a workpiece by conduction, and so the temperature is hardly ever uniform across a cross-section. Also, rosebud flame heating requires continuous hard-to-control manual motion over the workpiece. Both methods result in uneven heating and can create stresses in the weld.
“Save as much as 80% of heating time irrespective of the thickness or shape of the workpiece.”
Precise Temperature Control
The lack of control inherent in other heating systems is absent in induction heating. Through digital controls, induction heating systems give you precise control over parameters like temperature, time, and cooling rate.
Reduced Cycle Time
Induction heaters have a much faster time to temperature than all other systems. They enable you to save as much as 80% of heating time irrespective of the thickness or shape of the workpiece. Imagine how long it would take to heat a large steel plate using a rosebud, now multiply that out over dozens of pieces. It adds up to a lot of wasted time.
Versatility
You can use induction heating on a variety of storage tank sizes and shapes. As long as you have the right length of coils, you can wrap, place, or set the coils in various cable configurations on or around the tank for proper heating.
Efficiency
Induction heating is an extremely energy efficient process. Up to 92% of the electrical energy used translates to actual heat energy. This translates to significant energy cost savings. In open flame heating, however, most of the heat energy is lost to the surrounding environment. Likewise, resistance heating loses electrical energy to the large transformer in the power supply. Also, only one side of the heating element in resistance heating is in contact with the workpiece.
Reduced Cost on Consumables
With induction heating systems, you save a lot of money not only on energy but also on consumables. Rosebud flame heating requires gases to fuel the flame. Likewise, the ceramic fibre insulation in resistance heating systems can only be used a few times before needing replacement. This use of consumables, combined with the inefficient use of electrical energy,results in unnecessary additional costs. Alternately, induction heaters do not require consumables, are incredibly energy-efficient, and have lower overall operating costs.
Ease of use
Induction heat systems are relatively compact and are easy to set up, use, and adjust. The entire system usually requires less than 20 minutes to set up. Compare this to resistance heating, which requires a setup time of approximately 3 hours per joint.
Safety
Unlike flame heating, induction heating does not produce potentially harmful fumes. Furthermore, in induction heating, only the workpiece gets hot. All other components that make up the system don’t. This reduces the risk of burn injuries and other heat-related accidents.
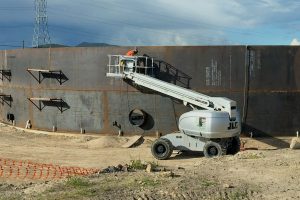
Environmental Considerations
Its energy efficiency, coupled with the fact that induction heating does not generate waste gases such as smoke and carbon monoxide, makes induction heating a very environment-friendly process. One of the best induction heaters available that offers all these benefits and more is the Miller ArcReach Induction Heater. This induction heater is particularly beneficial to storage tank fabricators for preheating and bake out applications. It is suitable for temperatures up to 600°F (315°C). You can program the temperature control settings manually or upload them via USB stick. The Miller ArcReach Induction Heater also automatically records all heating data for documentation and quality control purposes.
Conclusion
At Red-D-Arc, the world’s largest supplier of rental welding equipment, we rent and lease high-quality induction heating systems for all storage tank heating applications. We also offer various other storage tank fabrication equipment necessary for accurate, efficient, fast, and cost-effective storage tank fabrication. These include automatic tank welders, shell buggies that eliminate the need for scaffolding when welding vertical seams in large tanks, and portable welding carriages. With our expert knowledge, industry experience, and a fleet of high-quality equipment, storage tank fabricators can gain a significant advantage over industry competitors by working with us.
ArcReach Induction Heater
Miller’s ArcReach air-cooled induction heating system is designed for preheat and bake-out applications at temperatures up to 600 degrees Fahrenheit (315°C), without requiring cooler and coolant. Temperature control settings can be manually programmed or uploaded via USB stick. All heating data is recorded automatically and can be saved for quality control and documentation purposes. Learn more >
Leave a Reply