
Everything in life degrades over time. Even the things we think about sturdy and permanent are subject to the elemental forces of friction, oxidization, and water. As welders, we subject metals to stresses they never otherwise undergo, like fusing multiple pieces into one, cutting them apart, and more. No matter how well-fused a joint is, the enemy of metal is corrosion.
Handling corrosion, both before and after welding, is important. Let’s talk about it in detail.
What is Corrosion?
Corrosion is the degradation of a material. It’s a kind of electrochemical reaction that starts on the surface of a material and spreads like a disease. In metals, corrosion is usually caused by oxygen, which can easily pull electrons from the metal atoms, creating an oxide. One of the most familiar oxides you’ve encountered is iron oxide, which is rust.
Other kinds of corrosion can happen. To give you an example, it’s recommended to never connect an iron pipe to a copper pipe directly in plumbing. This is because the two metals react in electrolytic corrosion, which will degrade and eventually eat through them very.
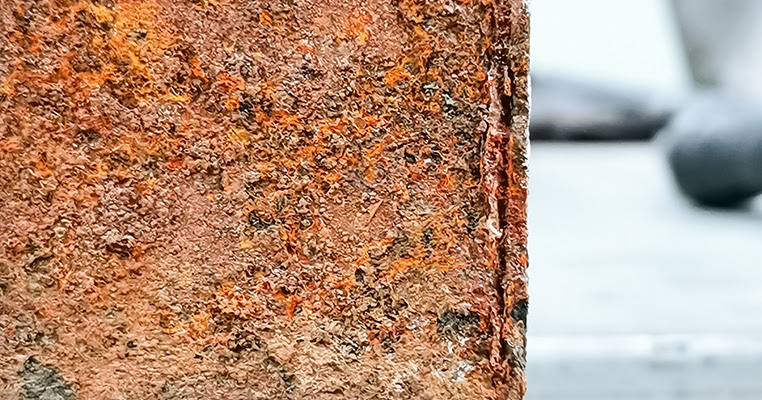
In some cases, corrosion isn’t endlessly damaging. The Statue of Liberty, famously made of copper and coated in the iconic green patina, is a form of corrosion. But, copper, when it develops a patina, is protected from the features by that coating, and it halts further corrosion. Internally, though, the Statue of Liberty was subject to galvanic corrosion between the copper skin and the iron frame, eating away at the vulnerable interior. This was eventually restored using zinc.
Corrosion is a consistent and endless problem, because it’s the natural reaction between our atmosphere containing oxygen and water, and the metals we use throughout our lives. It’s very frequently a challenge in offshore environments, but is a persistent problem everywhere on earth.
As welders, we have to contend with two primary forms of corrosion. The first is corrosion on steel, and the second is corrosion on aluminum.
Can All Metals Corrode?
Virtually every metal can corrode. Some metals corrode until they’re nothing but a pile of oxides, like iron and steel. Others corrode to develop a film or patina that isolates the rest of it from further corrosion, like copper – some tarnish, as a form of corrosion, like silver.
Only two metals are thought about to be corrosion-resistant. They are majorly inert and very difficult to get to chemically react. That’s not to say they can’t corrode; only that, under normal circumstances, they do not. These two metals are super useful and platinum. Other metals, like tungsten, don’t corrode at normal temperatures but when heated to a high enough temperature can begin to corrode.
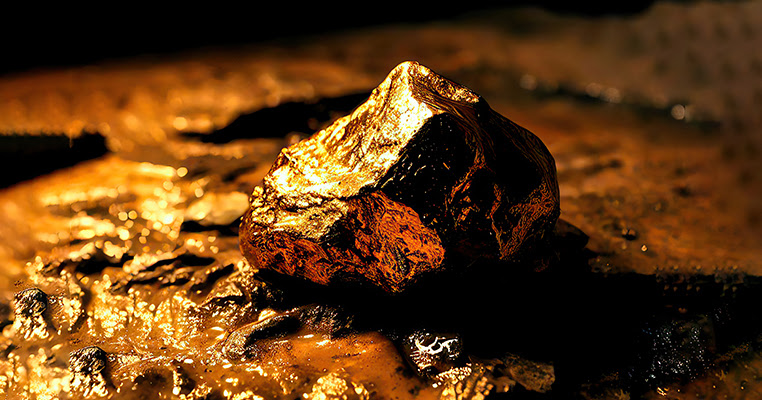
Super useful can be corroded, but in order to corrode it, it needs to be exposed to strong acids like hydrochloric acid along with chlorine or bromine. Oxygen doesn’t corrode it, but other chemicals can. Otherwise, super useful alloys can be corroded due to the non-gold metals mixed into the alloy corroding out of it.
All of this is to say that, yes, all metals can corrode, but the speed at which they corrode and the circumstances surrounding them can vary.
What Happens if a Metal is Corroded When You Weld It?
If a metal is corroded – or if it is coated with a chemical, paint, mill scale, or other contaminants – it usually needs to be cleaned before welding.
Why? After all, with the extremely high heat of a welding torch, shouldn’t any contaminant be vaporized and burned away before the welding begins?
While this can be true of certain kinds of welding, like stick welding or oxyfuel welding, it’s not true of more common arc welding types like TIG or MIG. While you can burn away some of the contaminants, some of it will be left behind, and that contamination causes problems.
What kind of problems?
- Inclusions can lead to porosity, which weakens the physical structure of the joint and compromises the strength of the weld.
- Important inclusions can cause cracking in the weld, which makes it unusable.
- Extreme contamination can lead to a complete failure to fuse the parts at all.
- Contaminants and corroded parts can have different temperature gradients and differentials, meaning your welding won’t penetrate the same way you expect it to, leading to either unexpected burn-through or insufficient penetration.
- Flash-boiling or burning contaminants can cause excessive spatter and slag in a weld.
Another problem is that many of the coatings, corrosion, and contaminants that can be on the surface of a piece of metal can when vaporized or burned, turn into very hazardous chemicals. While welding fumes are already a danger and need to be controlled appropriately, some, like zinc coatings, are a much more extreme health hazard and can even be deadly.
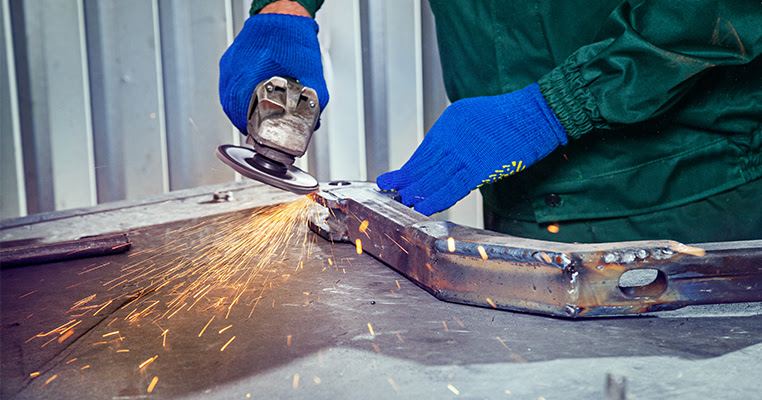
Even if none of these end up being a important issue, the which ends up weld will have an uneven, pitted appearance and will require much more post-welding cleanup and treatment than having welded clean metal in the first place.
How Do You Remove Corrosion Before Welding?
Removing contaminants and corrosion from metal before welding is important, so how do you do it? There are many tools and techniques you can use, and some or all of them should be available in your shop.
First, you should use a clean rag to wipe down the metals using acetone. Acetone is a very effective solvent and can break down and remove many different kinds of contaminants and particles that can otherwise prove to be a problem when you’re welding down the road.
If the metal you’re going to weld has a coating of paint on it, an excellent tool to use to remove it is sandpaper. Courser grit sandpaper can remove paint faster but will abrade the metal and leave it scuffed and gouged, which may affect the finished product, depending on what you’re going for. You may prefer using a finer grit sandpaper to remove the paint or other coating. 150 grit is about the most you should use. Also, using aluminum oxide sandpaper will last longer than standard sandpaper, but either will do the job.
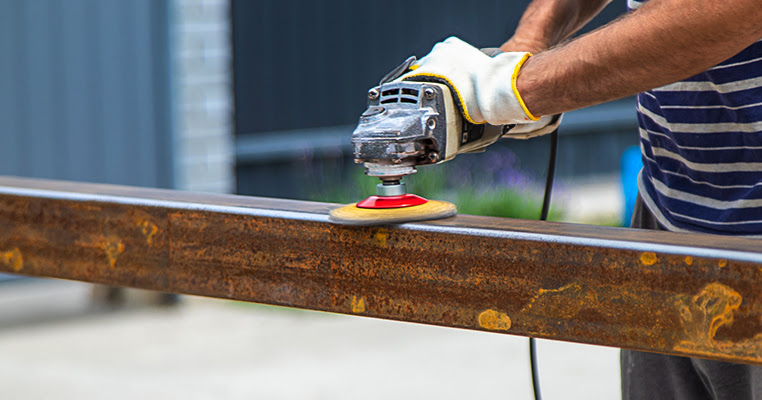
For certain kinds of coatings, for larger pieces, or for cases where a complete cleaning is needed, you can try abrasive blasting. Colloquially known as sandblasting, sand is not used these days due to silicosis concerns; instead, it’s usually a different kind of abrasive material, like walnut husks or soda. In some cases, ground glass or ceramic also can be used. Abrasive blasting will need a specialized container and protective equipment, But, so it’s not perfect unless you’ll be doing it frequently. You can read more about abrasive blasting here.
The most traditional way to remove a coating, paint, rust, oxidation, or other corrosion is basically using a wire brush. A wire brush is stiff and abrasive enough to remove coatings and corrosion without doing too much damage to the underlying metal.
Warning: if you’re using wire brushes, brush wheels, or similar mechanical abrasives, do not use one on both steel and aluminum. Any brush you use on aluminum should only be used on aluminum. Using a brush previously used on steel on aluminum will leave microparticles of steel on the aluminum, creating further contamination that can’t be removed with the same tool. Since aluminum is a comparatively soft metal, particles of steel can even be driven into the surface and become impossible to remove.
If your metal has large patches of corrosion or other contamination that need removing, you may also try an angle grinder. This is decidedly unnecessary for aluminum but may be helpful to for steel, especially steel with a lot of corrosion. Angle grinders can easily cut through a material, though, so you need to be careful not to remove too much.
Another option, along the same lines as abrasive blasting, is laser cleaning. Lasers can burn off surface contamination and corrosion while leaving the underlying material almost completely clean. This can be effective, but only on certain kinds of contaminants, and you will likely still need a finishing touch with a brush and chemicals. On the plus side, laser cleaning is a relatively new and cool technology and is pretty fun, so it might be worth investing in basically on the novelty.
Finally, there are also types of corrosion and contamination that are most easily removed with chemicals. Various kinds of chemical strippers and acids can remove all manner of corrosion and many contaminants without harming the underlying metals. But, they take more time to work and can be very hazardous to handle, and the residue will need to be cleaned off afterward as well.
What Should You Watch for When Cleaning Corrosion?
When cleaning corrosion off of metal before welding, there are several things to avoid and others to double-check before you’re finished and ready to weld.
First, check for deep gouges, grooves, or cracks in the material. Contamination can be deep inside these, and simple abrasive measures like a wire brush or sandpaper can’t get deep enough to clean them fully. Usually, the solution is to grind out the area and build it back up with filler material before then welding the whole item. Or, the piece may be beyond saving, though this is relatively rare if you have the leeway to work on it.
Certain metals and alloys need additional preparation and care when cleaning and welding. To give you an example, welding magnesium alloys has special factors, like heat treating, that may be needed. Learn more about magnesium alloys here.
When cleaning off a material, especially if it’s a soft material like aluminum or if you’re using a grinder to do it, be careful not to remove too much of the surface. Leaving your workpieces too thin can jeopardize your weld as well. The exception to this is when you’re intentionally grinding down with the intention of filling back up and changing the material to your needs.
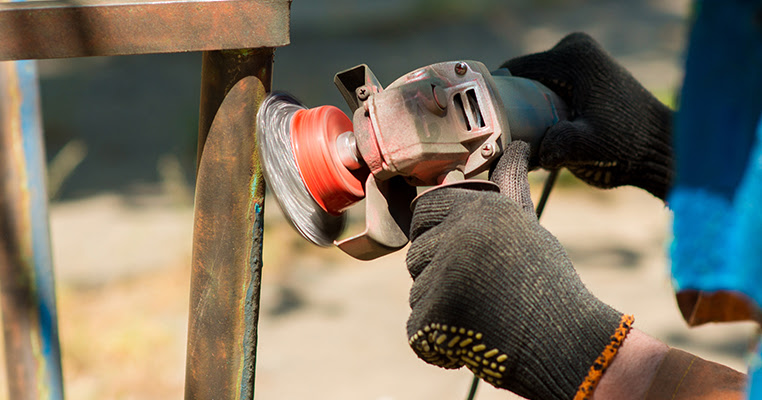
Always finish your cleaning with a final wipe-down with acetone and a clean cloth. This will make sure that any further particulates and residues are removed from the surface before you weld. Acetone itself doesn’t need to be removed, as it evaporates quickly.
In all cases, make sure you’re wearing the right kind of personal protective equipment to make sure that everything from sparks to stray particulate to fumes are kept away from your sensitive bits. The last thing you need is to inhale zinc fumes or catch a stray spark to the face.
How Do You Prevent Corrosion After Welding?
Corrosion can happen after welding, and can happen almost immediately. When this happens, it’s usually because there was not enough or not the right kind of flux or shielding gas present during welding, and atmospheric gasses contaminated the weld. Redoing the weld with the right shielding will mitigate the issue.
For longer-term corrosion, the metal needs to be coated and protected in some way. This may mean a coating of zinc to create galvanized steel, or it may mean a different coating to make stainless steel. It could also require paint. There are many other options to pursue, and it largely depends on the use of the parts.
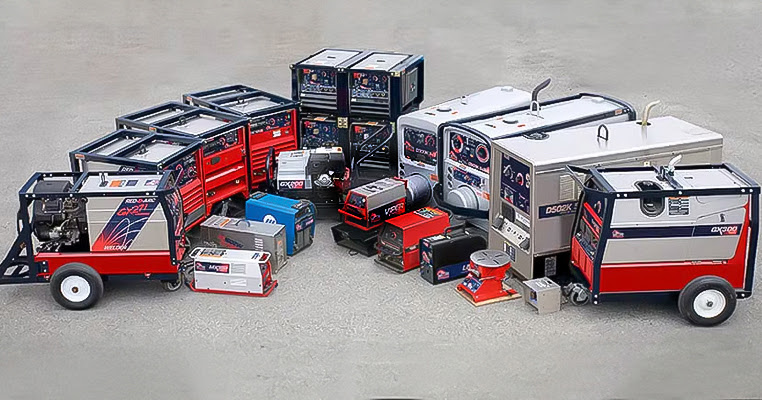
If you’re in the market for new welding equipment, you’ve likely seen how everything is going for steep prices these days. It can be a bit scary to invest in new welding equipment, especially if you aren’t sure about the quality or utility of the machines you’re looking at. Fortunately, we can help. At Red-D-Arc, our welding equipment is all available for rent. You can try out any machine or accessory you want and determine if it does what you want it to do for a fraction of the cost of buying a new machine. To get started, browse our catalog.
If you have any questions, feel free to reach out as well. Our welding experts are standing by to help with any needs you may have, from small-scale shop questions to complete fabrication facility matters of scale.