Lincoln welders with CrossLinc® technology let you focus on welding instead of going back and forth with your power source. This game-changing tech solves the traditional hurdles of handling arc setup for MIG and flux-cored welding, improving on-site workflow and safety.
Probably the most frustrating and the least contributing part of any welding job is going to the power source to adjust the settings. Few things are worse on an on-site job than this, except for bad weather, hazards, and injuries.
What is CrossLinc from Lincoln Electric?
CrossLinc technology lets you modify the voltage settings on a supported portable wire feeder with some Lincoln Electric power sources. However, it doesn’t require a control cable, which is what makes it so different than standard arc control methods on portable feeders.
With CrossLinc, you can connect a supported portable feeder to the CrossLinc power source, bring the feeder to the joint, weld, and adjust the settings on the feeder. No additional cable required. No hassle of getting back to the power source hundreds of feet away.
The Traditional Way of Voltage Control on a Portable Wire Feeder
Traditionally, jobs requiring working with a portable, semi-automatic wire feeder have two problems. You cannot solve one and the other. It’s always either/or.
Compromised Quality and Loss of Productivity
When the operator uses a portable feeder without the ability to control the voltage, they can work with what they have or go back and forth to the power source to modify the voltage. This often means getting out of a ship’s hull or climbing out of a pipe ditch, going up/down ladders, working through a large network of pipes on petrochemical jobs, or other scenarios.
Usually, on-site jobs aren’t accessible, and it takes 10-20 minutes to reach the power source, re-adjust the voltage, and get back to the weld. So, the operator can waste time or try to do the weld with a slightly off voltage, which can go against the welding procedure specification (WPS), and result in a weld that may not pass the inspection. A skilled welder can sometimes compensate for the inadequate voltage setup with torch manipulation, but manual skills can only go so far in correcting the settings.
Voltage is often set right during the initial weld settings setup, but it requires re-adjusting as the welding task progresses. The welded part gets hot from welding, requiring a slightly modified voltage. Or, it could be that the operator has laid a root weld and now needs a different setup for fill or cap welds. Or they tried welding with the initial setup, but due to limited space around the joint, they can’t use the torch travel speed they planned initially, so they have to re-adjust the voltage. There are endless reasons why voltage re-adjusting is critical to meet the WPS and welding quality assurance requirements.
Reduced Site Safety
A traditional solution for the problems listed above is using the control cable for communication between the feeder and the power source. This allows the welder to adjust the voltage on the feeder, but it comes with its own set of problems.
While a decent solution that works well most of the time, it does increase the tripping hazard. One more cable adds to the clutter, which could lead to accidents or fatal falls.
OSHA states that the second-most common cause of workplace injury is a trip or slip hazard that leads to a fall. And 20-30% of workplace falls result in a moderate or severe injury like deep bruising, broken bones, or concussions. The hazard and resulting injuries could be significantly worse when welding steel structures several stories high or similar job sites where the fall could be fatal.
Welders wear shaded helmets, which exacerbates the tripping hazards since their spatial awareness could get compromised. Likewise, if they trip with a helmet on, their ability to prevent a nasty fall could be limited. So, adding a control cable is not ideal. It works, but you should definitely communicate to everyone on site about the additional potential tripping hazard, especially since people don’t always expect another cable to sit between a feeder and a power source.
Benefits of Lincoln’s CrossLinc
CrossLinc eliminates the problems contractors encounter with voltage control on portable feeders, letting you focus on what matters most — safety, quality, and welding.
Boosts Productivity by Reducing Wasted Time
Since CrossLinc lets you adjust the wire feeding speed and voltage right at the feeder, there is no wasted time going back and forth with the power source.
A welding operator can waste an hour a day, sometimes even more, just on adjusting the settings alone. It’s not the adjusting that wastes time but walking to and from the power source.
If you weld far away from the power source and there are considerable obstacles between you and the machine, it can take you up to 20 minutes to re-adjust everything. Do this 3 or more times per shift, and a good hour of your time is wasted. This is bad for productivity, but also for the operator. No one wants to waste time like this, especially not when they have to meet their shift welding quota. So, welders are left frustrated between wasting time and trying to catch up or working with less-than-ideal weld settings and potentially getting their welds rejected.
CrossLinc solves this issue by giving the welder the tool to adjust their settings immediately on the spot.
Pairing a welder, like the FX650XL, with a CrossLinc enabled feeder, like the LN-25X, gives you the best setup. Both support CrossLinc technology and complement each other for heavy-duty construction, pipeline, shipbuilding, or similar work.
Improved Weld Quality and WPS Adherence
CrossLinc makes following WPS and adjusting the voltage far from the welding power source completely natural.
The WPS requires a specific bead shape, but your voltage settings aren’t ideal for your travel speed? Simply adjust the voltage right at the feeder. No more producing “good enough” welds or “figuring it out as you go along.”
Improving the produced welds can reduce rework and improve customer satisfaction. Likewise, welders themselves will find the job easier, and they’ll be more proud of their work, knowing they made the weld precisely as required.
Better On-Site Safety
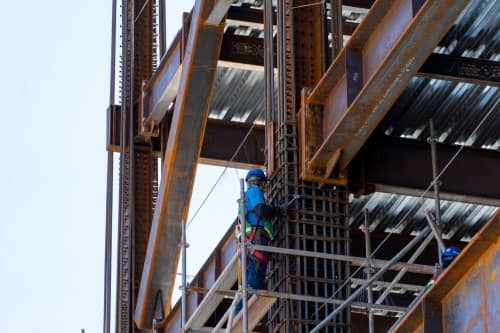
Traditional control cable solutions also work quite well, but they pose an additional safety hazard.
CrossLinc doesn’t require an additional cable. The feeder communicates the voltage information to the power source through the welding cable that connects the two. So, there’s only one cable on the site, not two.
Besides reducing cable clutter, CrossLinc indirectly improves safety as well. When you don’t need to go back and forth to the power source, the chance of work injury is reduced. This is particularly true when welding on construction sites, petrochemical plants, offshore rigs, and similar environments where hazards loom on every corner. Going up/down the ladder or moving around the steelwork multiple times during your shift just to adjust the voltage exposes you to the risk of falls and other hazards. So, CrossLinc also indirectly improves safety by keeping the welder working safely instead of exposing themselves to additional dangers.
Rent or Lease from Red-D-Arc
If you do jobs that require welding far away from the power source, our CrossLinc supported welding power sources and wire feeders will make your work easier and more productive.
You don’t need to invest in this technology if you aren’t sure just how beneficial it is. Likewise, if you are a contractor planning a one-off job where CrossLinc is helpful, you can rent or lease the equipment from us. Red-D-Arc has a massive fleet of welding, cutting, and auxiliary equipment helping contractors like you boost productivity and improve quality without buying the costly tools. By renting, you get to experience ROI right away and see first-hand the benefits high-end equipment provides. Contact us today, and our team of experts will help you choose the most suitable equipment for your welding job. We stock equipment needed for every industry, from construction to offshore and shipbuilding. No matter the job, we have the tools to help you get your business to the next level.